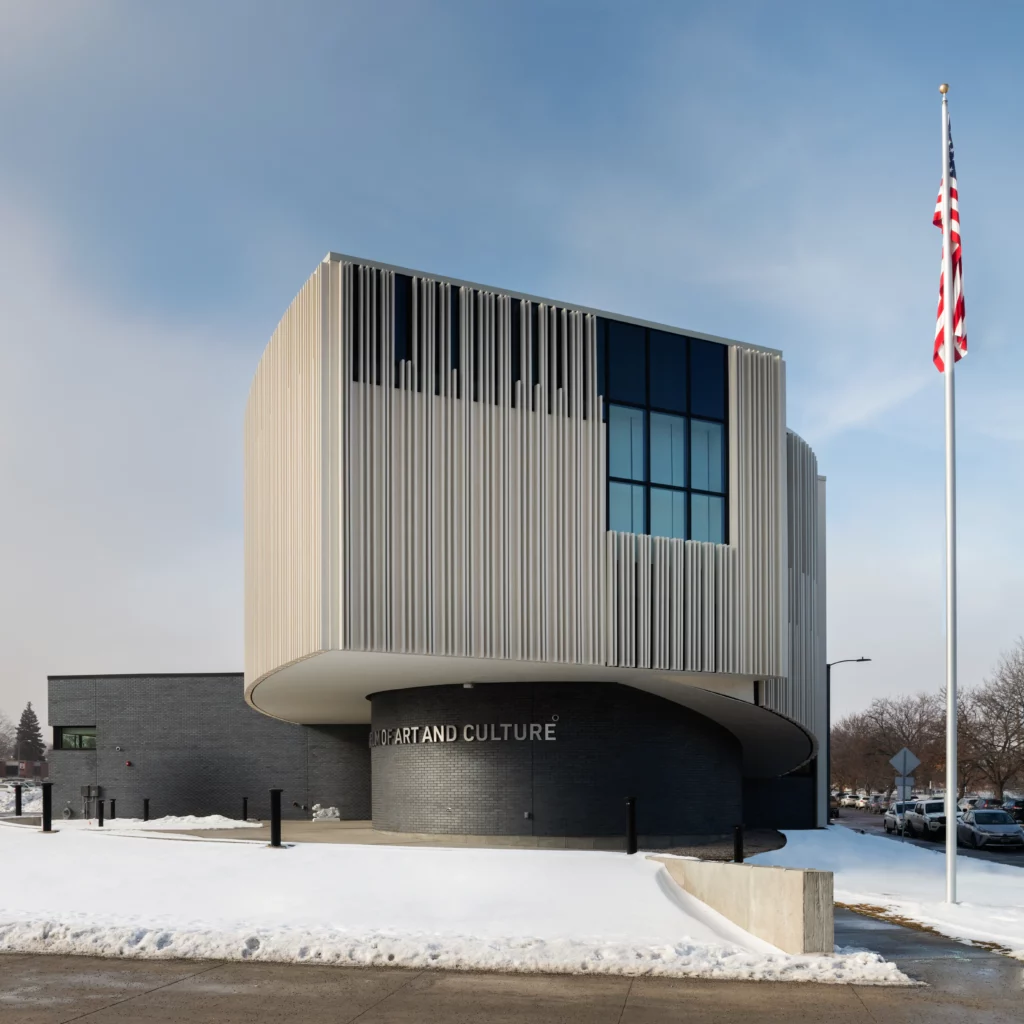
Table of Contents
Longboard Architectural Products is renowned for its innovative approaches in the construction industry, particularly in creating sustainable building solutions.
Among their standout offerings, the HITCH™ Cladding Attachment System exemplifies a commitment to energy-efficient building practices.
This article explores how the HITCH™ design, material composition, and integration capabilities contribute to creating high-performance facades crucial for today’s, and tomorrow’s energy-conscious architectural projects.
Overview of HITCH™ Cladding Attachment System
The HITCH™ system represents a revolutionary advancement in cladding attachment technology. Engineered to both dramatically reduce thermal bridging, while also having significant structural capabilities—both persistent challenges in façade construction—it has been certified as an advanced component by the Passive House Institute. This system combines modularity, superior thermal efficiency, and robust loading capabilities to improve the thermal performance of the entire building envelope.
Design Specifications
Modular Design Flexibility
The modular design of the HITCH™ Cladding System allows for significant flexibility in accommodating various architectural designs. This adaptability is achieved through adjustable components that can be configured to different depths and alignments, accommodating a broad range of façade geometries and design aesthetics.
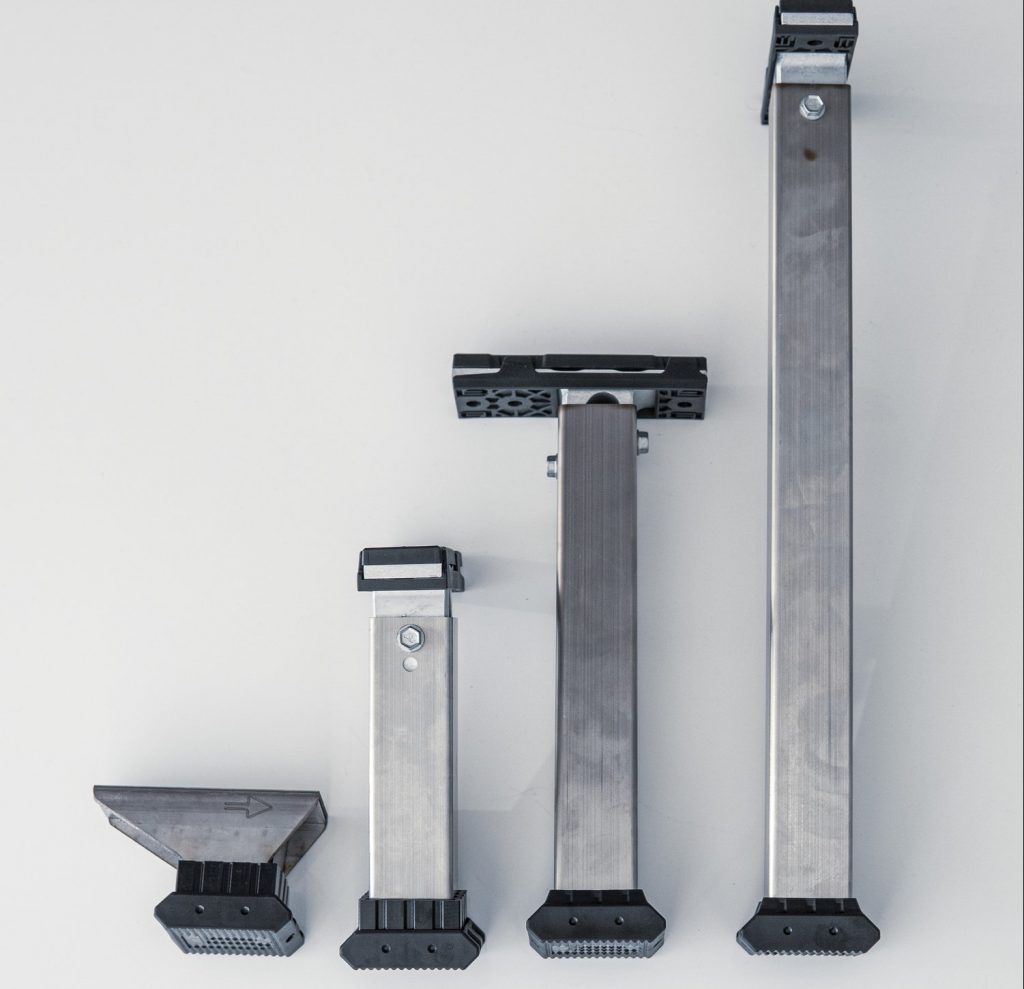
Dimensions and Tolerances
The system’s components come in a variety of standardized sizes, with precise tolerances that ensure compatibility across a broad spectrum of building designs. These dimensions facilitate seamless integration with different façade materials and insulation thicknesses, supporting custom solutions tailored to specific project needs.
Materials and Construction
Constructed from durable materials selected for their robustness and load-bearing capabilities, the HITCH™ system’s components are designed to ensure longevity and sustained performance. The materials chosen not only uphold the structural integrity of the facade but also enhance its sustainable qualities, aligning with modern green building standards.
At the core of HITCH™, the base is made from high tensile aluminum, which is capable of supporting cladding loads of up to 15 psf. This is complemented by an adjustable tube crafted from stainless steel, known for its excellent strength and relatively low thermal conductivity of 15 W/(mK). Together, these materials provide the system with exceptional loading capabilities under conditions of high wind, dead loads, and seismic activity.
Thermal Bridging Reduction Techniques
The materials used were chosen not only for their structural properties but also for their ability to manage thermal energy effectively. Unlike traditional materials that may have higher thermal conductivities, the selection in the HITCH™ system allows for the careful control of thermal bridging.
Strategic placement of thermal breaks within the system further reduces energy transfer, ensuring minimal contact between dissimilar materials and effectively managing the path for thermal energy. This approach significantly enhances the energy efficiency of the system while maintaining its structural integrity and performance.
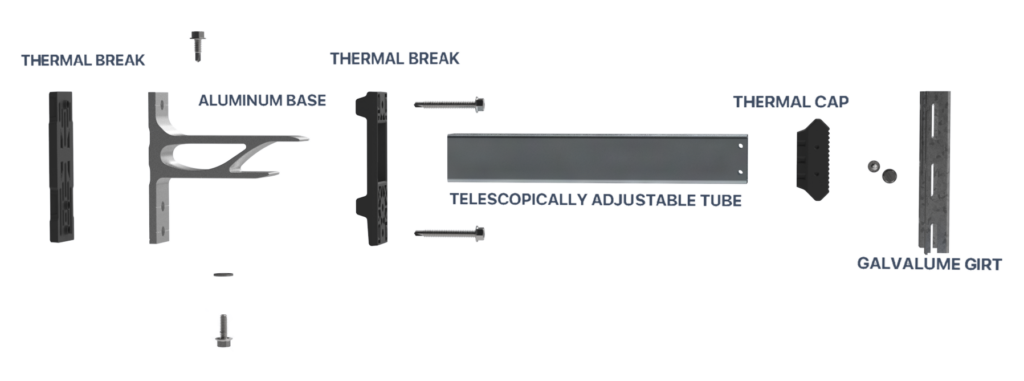
These thermal breaks are made from premium isolating materials that not only stop the contact between metals, but also completely isolate the fasteners from the aluminum.
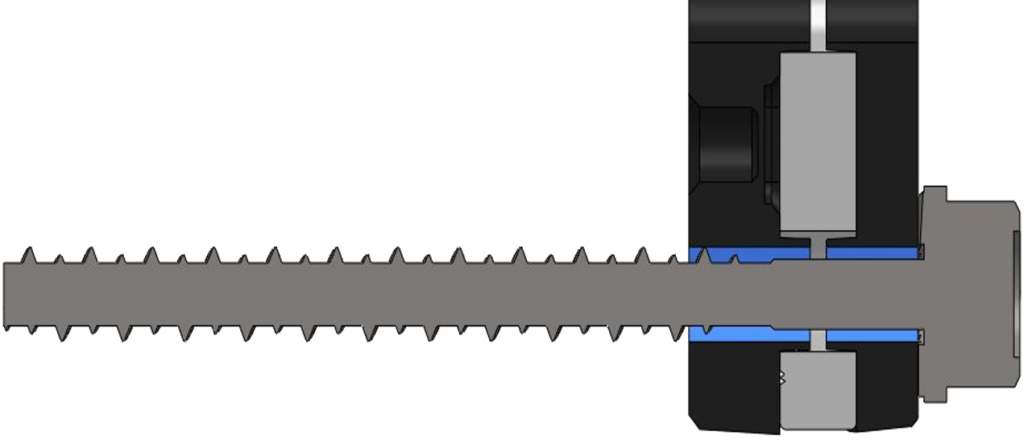
Combined with the thermal end cap, the entire system merges thermal performance with incredible loading capacity while maintaining direct mechanical fixture.
In total, with standard spacing of 32” by 48” HITCH™ can achieve up to 94% thermal efficiency.
Integration of Exterior Insulation
The HITCH™ system excels in integrating thick layers of exterior insulation, crucial for designers aiming for the highest levels of thermal performance. This feature is instrumental in enhancing the wall assembly’s R-value, thereby reducing energy loss and improving interior thermal stability.
The standard version of our system, HITCH™ SD, is capable of incorporating 2.5 inches of exterior insulation, while the HD and HD+ models can accommodate anywhere from 6 to 16 inches of exterior insulation.
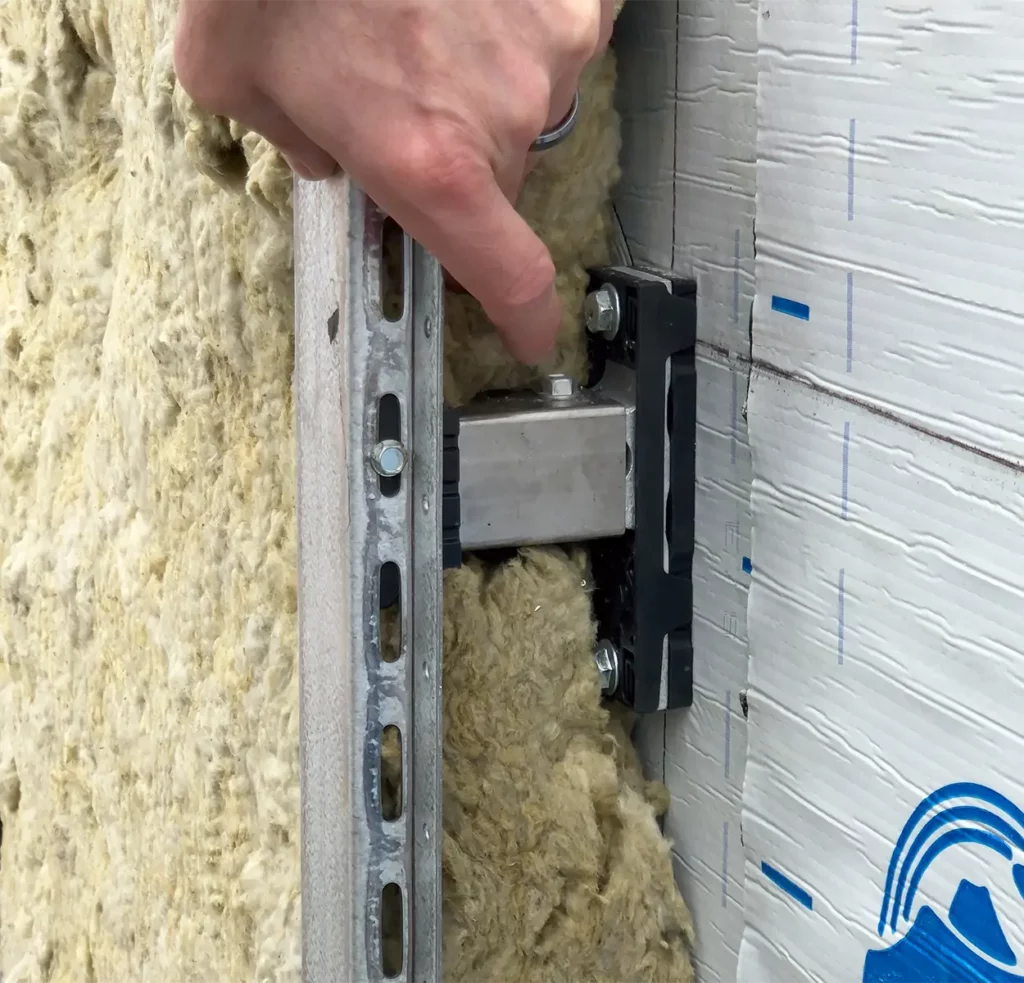
Case Studies
A prominent example of the HITCH™ system’s application can be seen in the Montana Museum of Art and Culture project. This case study demonstrates the system’s effectiveness in supporting large-scale exterior insulation requirements while maintaining a visually unique façade, which collectively contribute to significant energy savings and aesthetic enhancement of the building.
Comparison with Other Cladding Systems
When compared to traditional systems like Z-girts, the HITCH™ system offers superior performance in reducing thermal bridges and enhancing the insulation capabilities.
Through our own internal testing, we found a significant difference between the three designs:
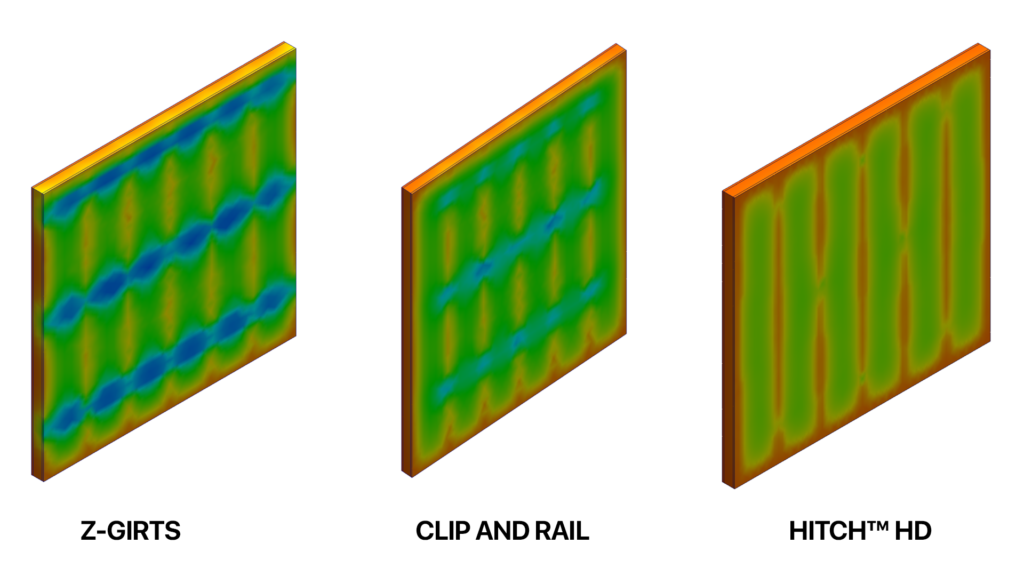
The main contributor to thermal inefficiencies in cladding attachments systems comes from the “slicing” effect many girt (and sometimes clip) systems are inherently designed with. This design effectively cuts through the exterior insulation, ultimately increasing areas of inefficiencies.
For designers looking to create thermally efficient facades without sacrificing creative vision, the following graph may be incredibly helpful.
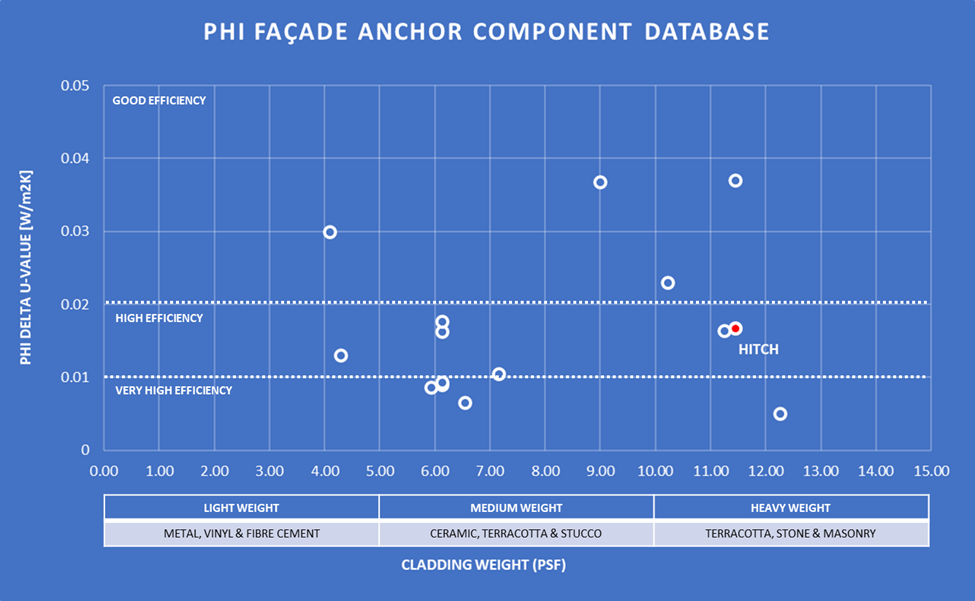
The data comes from the Passive House Institute Database of façade anchor components. The marketplace offers several alternatives, yet only a select few rival the efficiency and loading capabilities of HITCH™. Importantly, no other system matches the system’s modularity and constructability.
More in-depth thermal analysis can also be conducted, like the one below for HITCH™ HD+:
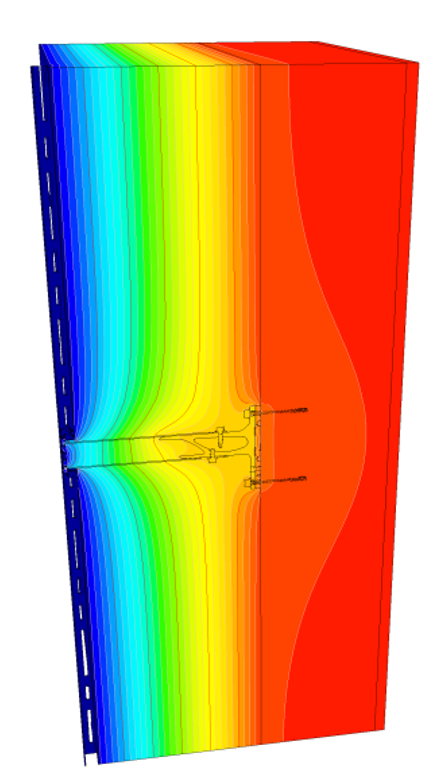
Installation Process
The installation of the HITCH™ Cladding Attachment System by Longboard involves a multi-step approach that ensures each component integrates seamlessly into the building’s façade for optimal performance:
Consultation and Layout
Assembly and Secure Fastening
Insulation Integration
Technical Support and Quality Checks
Longboard’s technical staff provide ongoing support throughout the installation, addressing any project-specific challenges. Final installations undergo rigorous quality checks to ensure all components are correctly installed, meeting the necessary thermal and structural requirements.
For a detailed step-by-step installation guide and additional technical support, please visit Longboard’s Technical Documentation.