2025 marks a major milestone for Longboard Architectural Products: 20 years of growth, innovation, and leadership in the architectural building materials industry. What began as a small coating operation in British Columbia has since evolved into one of North America’s premier manufacturers of premium architectural extruded aluminum products.
The story began in 2005, when founders Wayne and Mike partnered to offer specialty sublimation finishes for building product manufacturers. As they developed a deep understanding of the industry’s needs, Mike and his wife Karen saw an opportunity to do more than just supply finishes—they envisioned a complete aluminum cladding system that would combine the beauty of wood with the durability of metal. That vision materialized into the Longboard Cladding System. As demand surged and word spread about its unique aesthetic and performance, the Longboard brand quickly outpaced the original coatings business.
From that point on, Longboard focused on creating a comprehensive line of architectural products, all built around its high-performance finishing technologies. Interior and exterior systems—cladding, soffits, battens, and more—were developed with a commitment to quality, durability, and exceptional design. These products have become a preferred choice for architects and builders looking to achieve wood-inspired designs with non-combustible, low-maintenance materials.
By 2017, growth demanded expansion. The company built a new, state-of-the-art 350,000 sq. ft. manufacturing facility in Abbotsford, BC. Outfitted with advanced extrusion presses, a high-speed vertical powder coating line, and a precision sublimation system, the facility brought every stage of production under one roof. With high levels of automation and integrated quality control, Longboard ensured it could meet the increasing demands of North America’s architecture and construction markets.
In 2020, Mayne Coatings Corporation officially rebranded to Longboard Architectural Products, aligning the company name with its most successful and recognizable product line. Today, Longboard offers a robust portfolio of aluminum cladding systems, soffits, screens, ceilings, and custom architectural solutions for both exterior and interior applications—all manufactured in Canada using best-in-class processes and sustainable practices.
Longboard in 2025
Now, in its 20th year, Longboard stands as a leader in aluminum architectural systems. The brand is known for:
- Premium extruded aluminum products for cladding, soffits, screens & enclosures, ceilings and more
- Over 50 standard finishes, including woodgrains, solids, metallics, and innovative speckled textures
- Near limitless custom finish options
- Non-combustible, VOC-free, and Red List Free materials.
- ISO 9001 and ISO 14001Â certified operations.
- Passive House certified HITCHâ„¢ cladding attachment systems
- World class client support
From iconic towers like Vancouver’s Alberni by Kengo Kuma to thousands of residential, institutional, and commercial projects across North America, Longboard products continue to define modern architectural design.
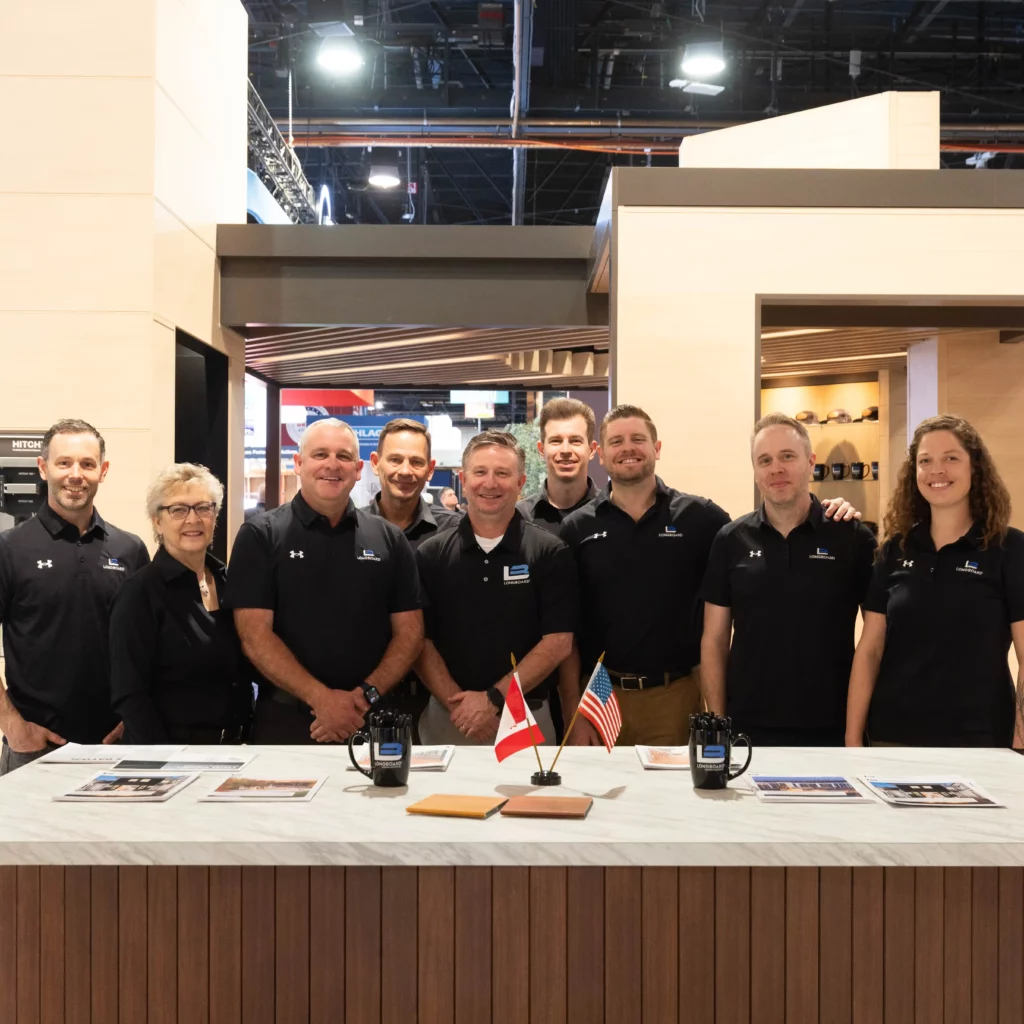
Manufacturing Process
Sourcing Aluminum
One of the most common questions we receive is: where does our aluminum come from?
We source from two key regions: Canada (primarily Quebec) and Australia. Notably, 96% of Canada’s aluminum production is powered by hydroelectricity—one of the cleanest energy sources available. This results in an average emissions intensity of just 2 metric tons of CO2 equivalents per metric ton of aluminum—six times lower than the global industry average. These emissions are 7 times lower than the aluminum produced in China, and 8 times lower than the aluminum produced in India.
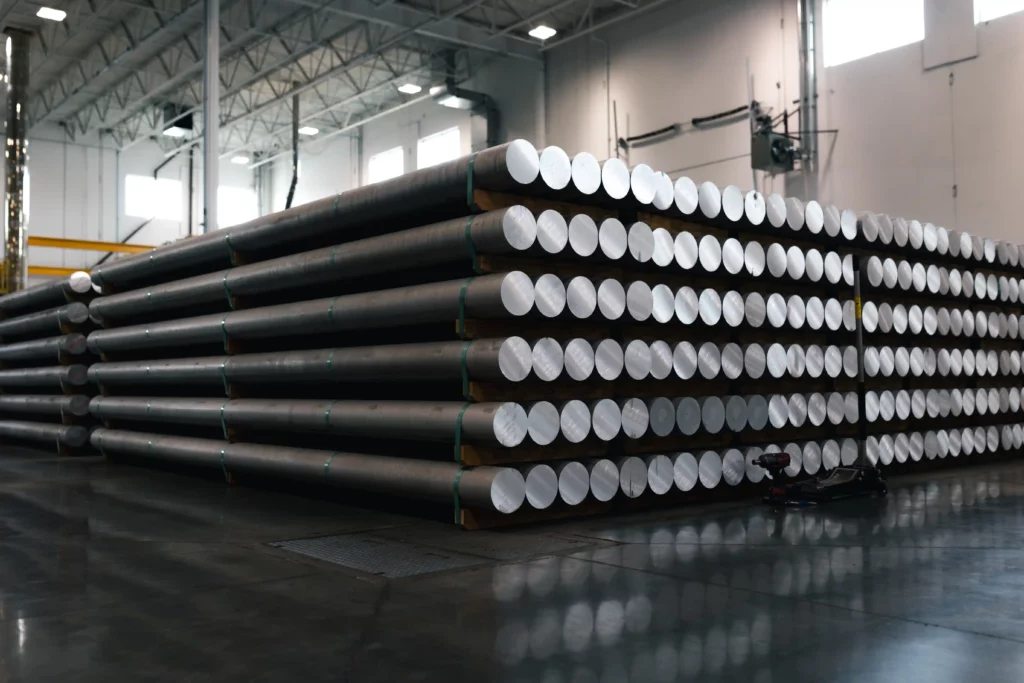
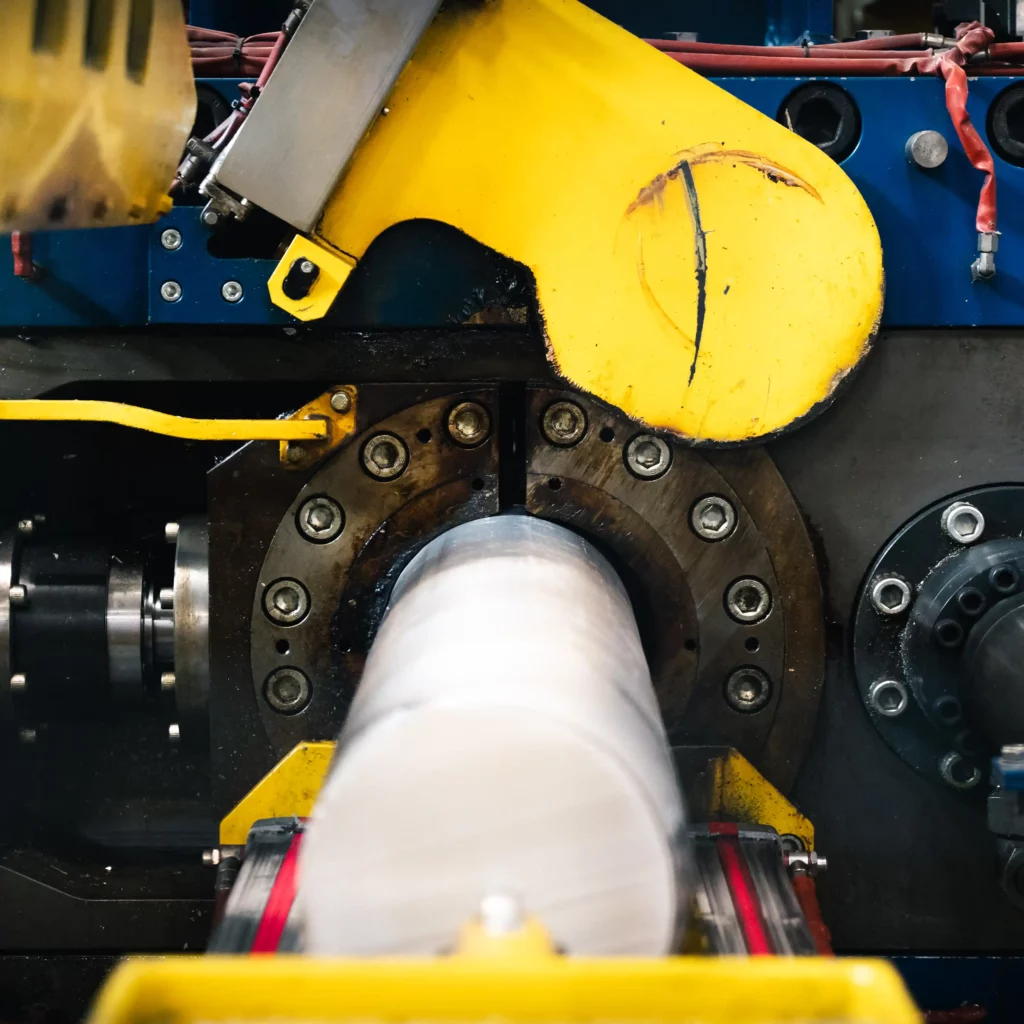
Shearing to Size
Our aluminum begins its journey as an 8″ diameter log. It is first heated to approximately 850°F, then sheared into billets. Each billet is pressed through a die—designed and tested in-house—which gives the aluminum its final profile. Every new product design begins with a custom die, built to meet Longboard’s strict performance and consistency standards.
Cooling & Aging Process
Each extruded profile, now over 200 feet long, is stretched to ensure straightness, then cut to standard 24′ or 12′ lengths. The profiles are then aged to achieve the required mechanical properties for long-term performance.
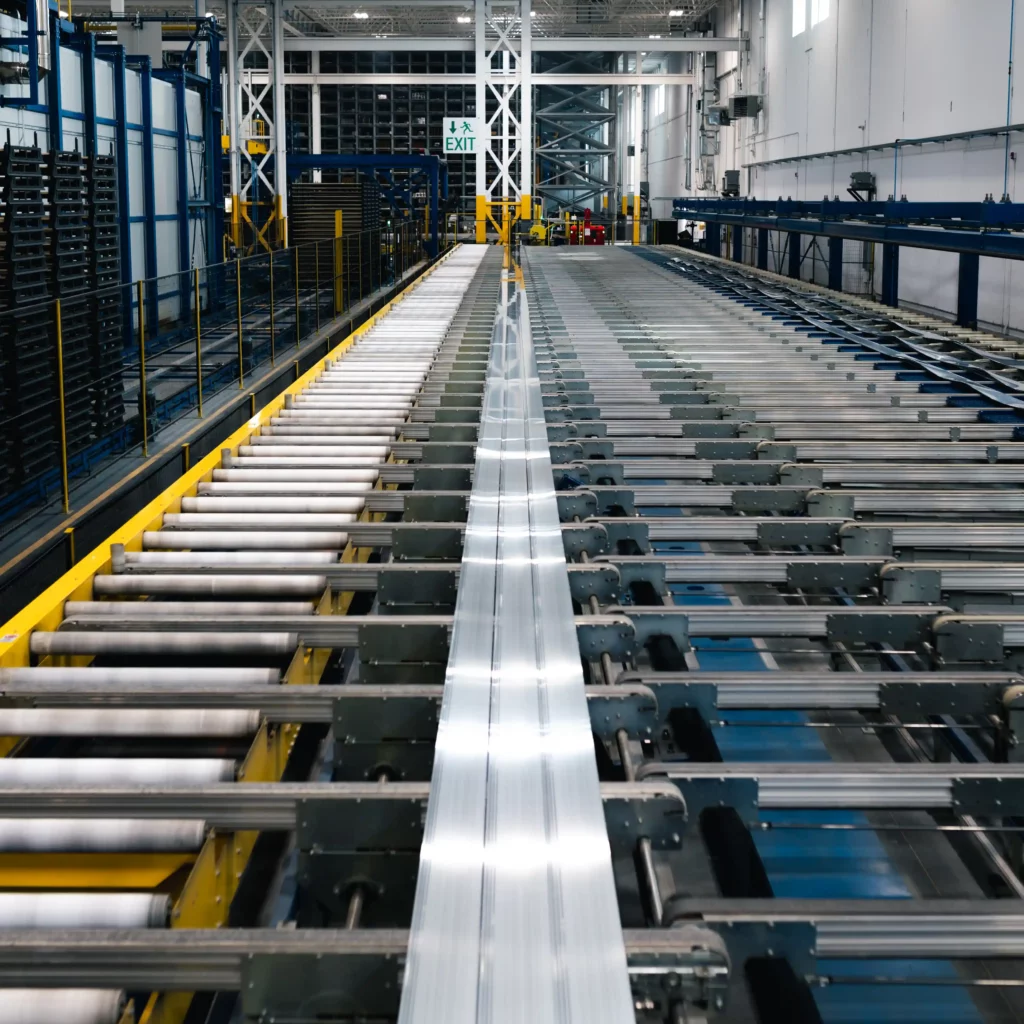
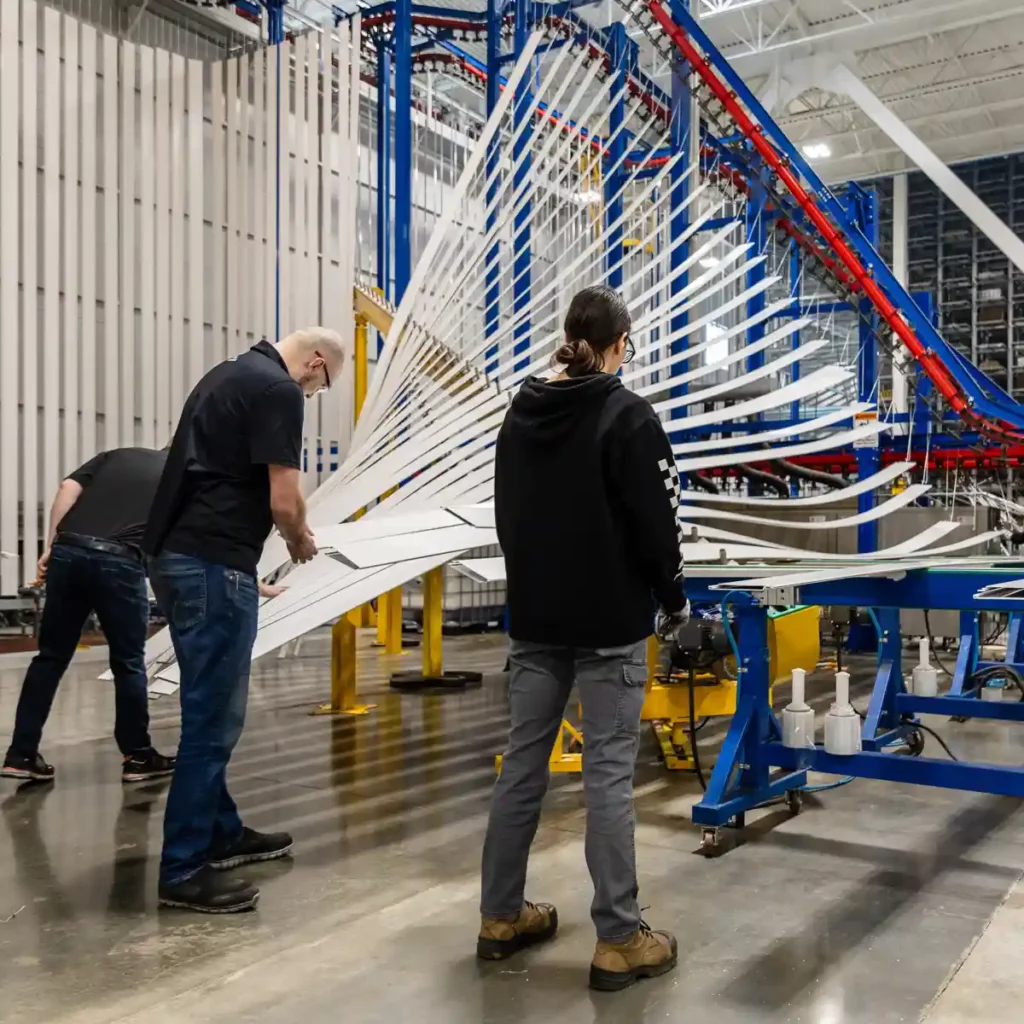
Powder Coating Process
Once aged, the profiles are cleaned and coated using our vertical powder coating line. Electrostatic spray guns apply a consistent, VOC-free powder that becomes the base finish for all Longboard products. For solid, metallic, and speckle finishes, this is the final step. The powder is cured in a high-temperature oven, resulting in a durable, weather-resistant surface that meets AAMA 2605 standards.
Sublimation Process
For woodgrain and naturally aged metal finishes, a second step is performed: sublimation. Here, a printed heat-transfer film is vacuum-sealed around each coated profile. In a specialized oven, the inks from the film are transferred directly into the powder-coated layer. This process delivers stunning wood and metal textures with all the durability and fade-resistance of powder coating.
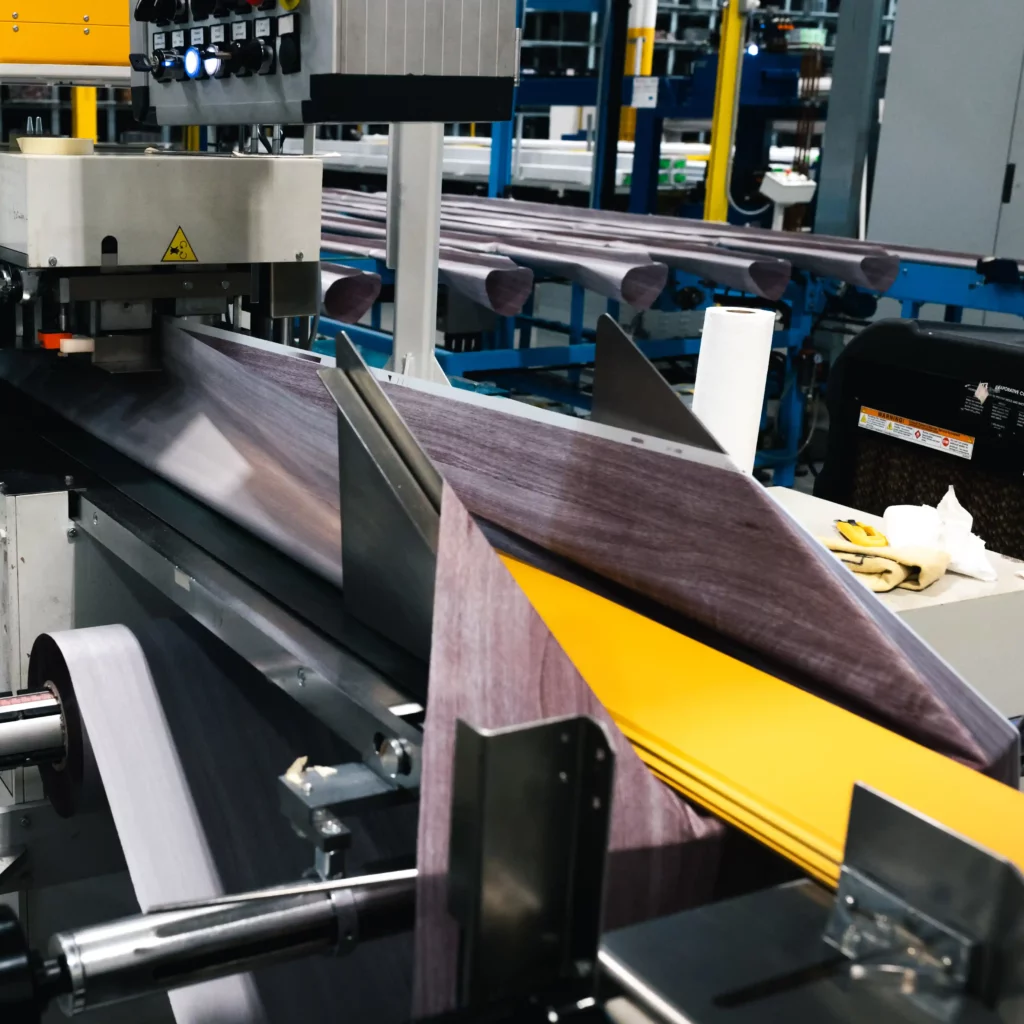
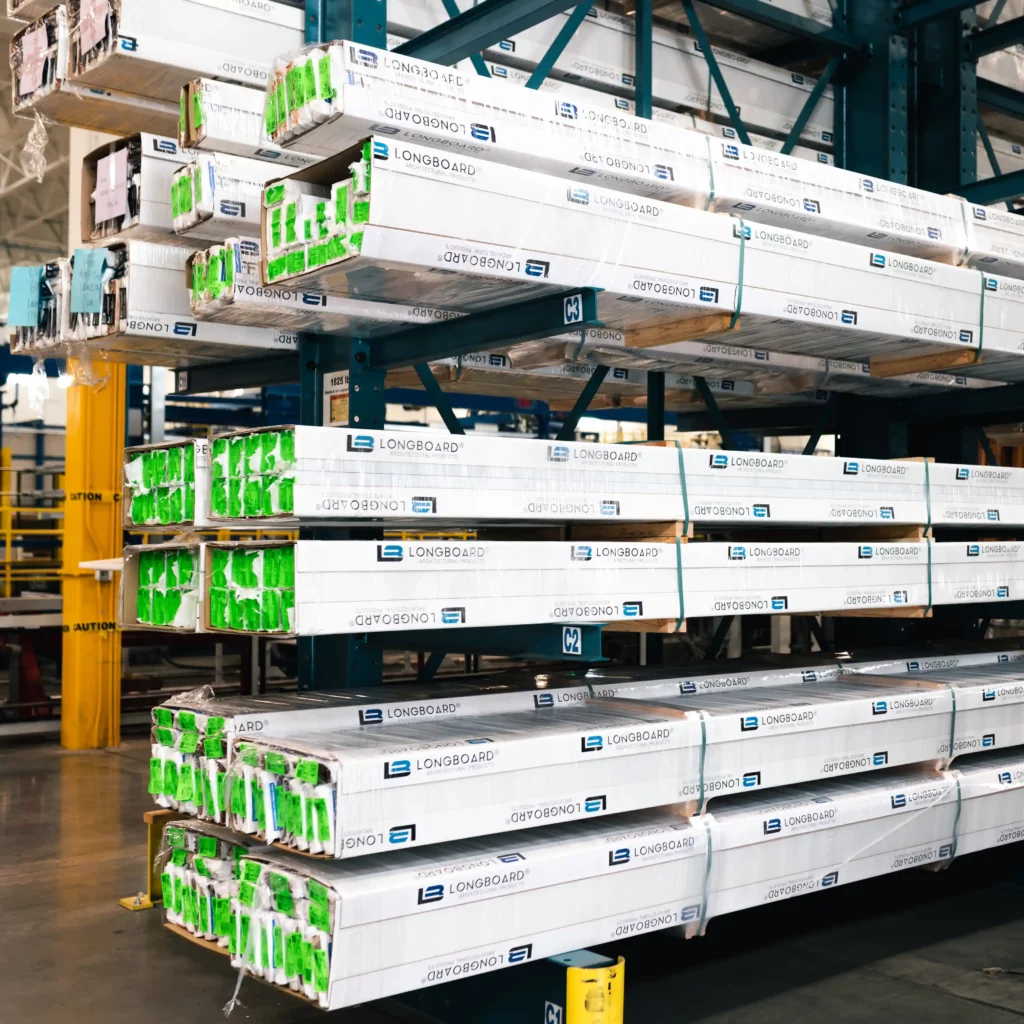
Packaging & Shipping
Finished products are carefully packaged and stored in a designated logistics zone within our facility. The building is designed to streamline transport, allowing carriers to load quickly and safely. We’ve optimized every stage to ensure products arrive in excellent condition and on schedule.
Quality Assurance
Quality is built into every step of our process. From the moment aluminum logs arrive to the moment finished profiles leave our facility, we conduct multiple inspections and automated checks to maintain high standards. Our ISO 9001 certification ensures consistent quality, while real-time monitoring across production lines minimizes errors and maintains efficiency.
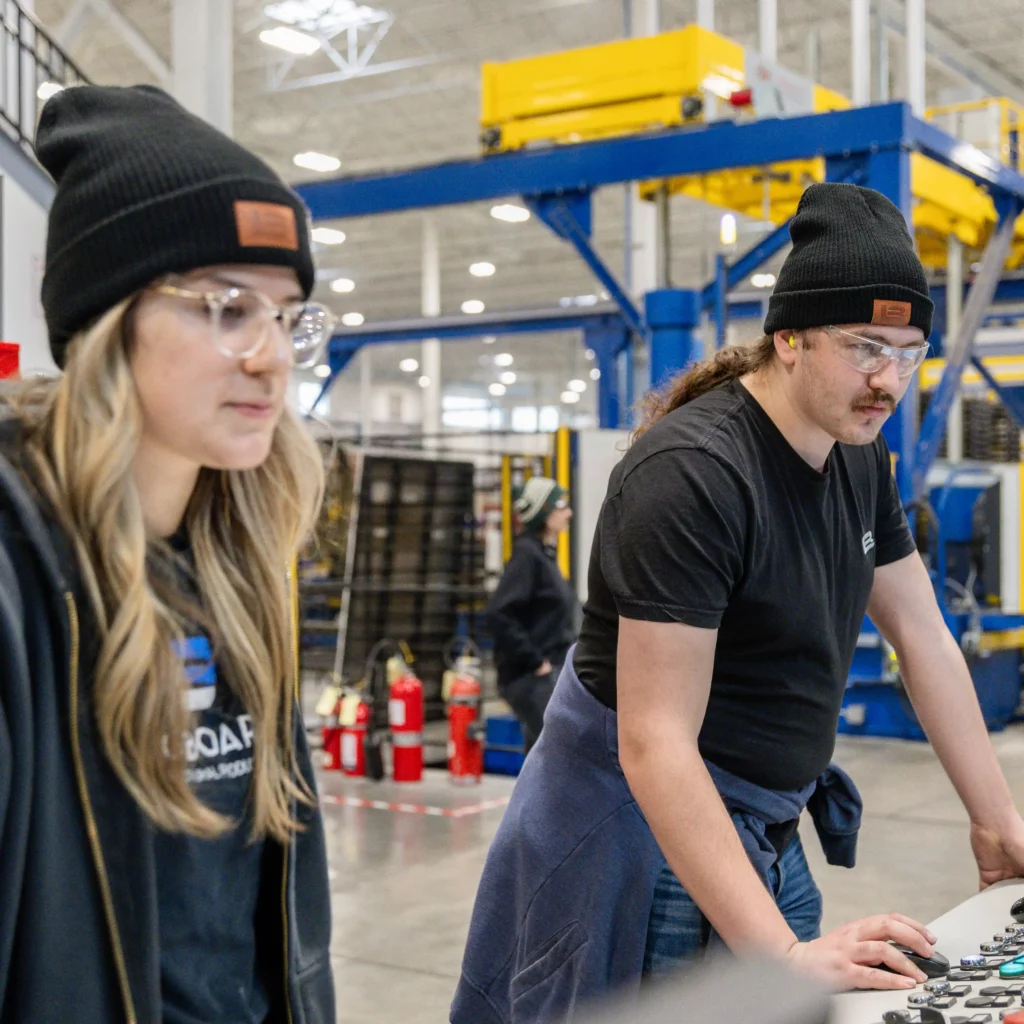
Preparing for the Future
As Longboard enters its third decade, our commitment remains unchanged: to inspire thoughtful design through innovation, sustainability, and craftsmanship. From a small finishing shop to a category-defining manufacturer, our journey has been shaped by the architects, builders, and communities who continue to choose Longboard. Here’s to the next 20 years of changing the face of architecture—one project at a time.
Gallery
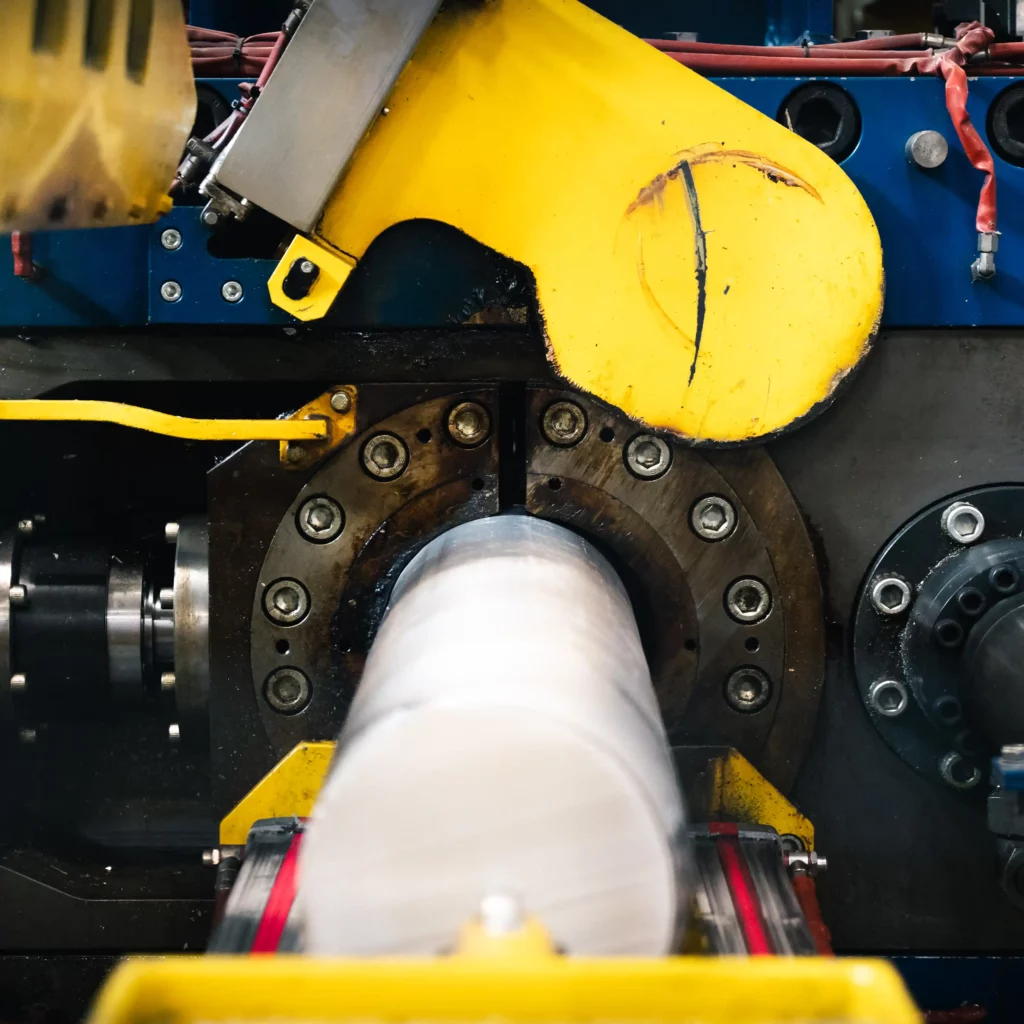
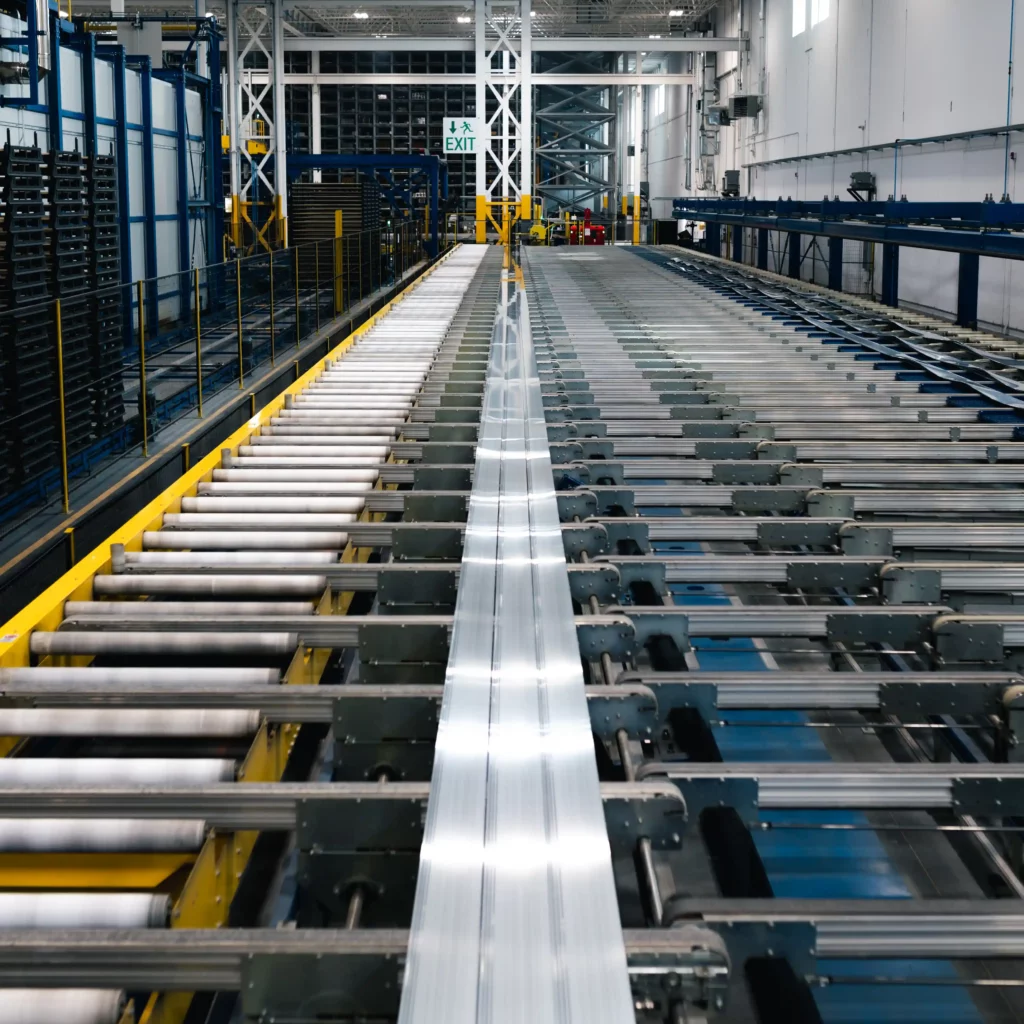
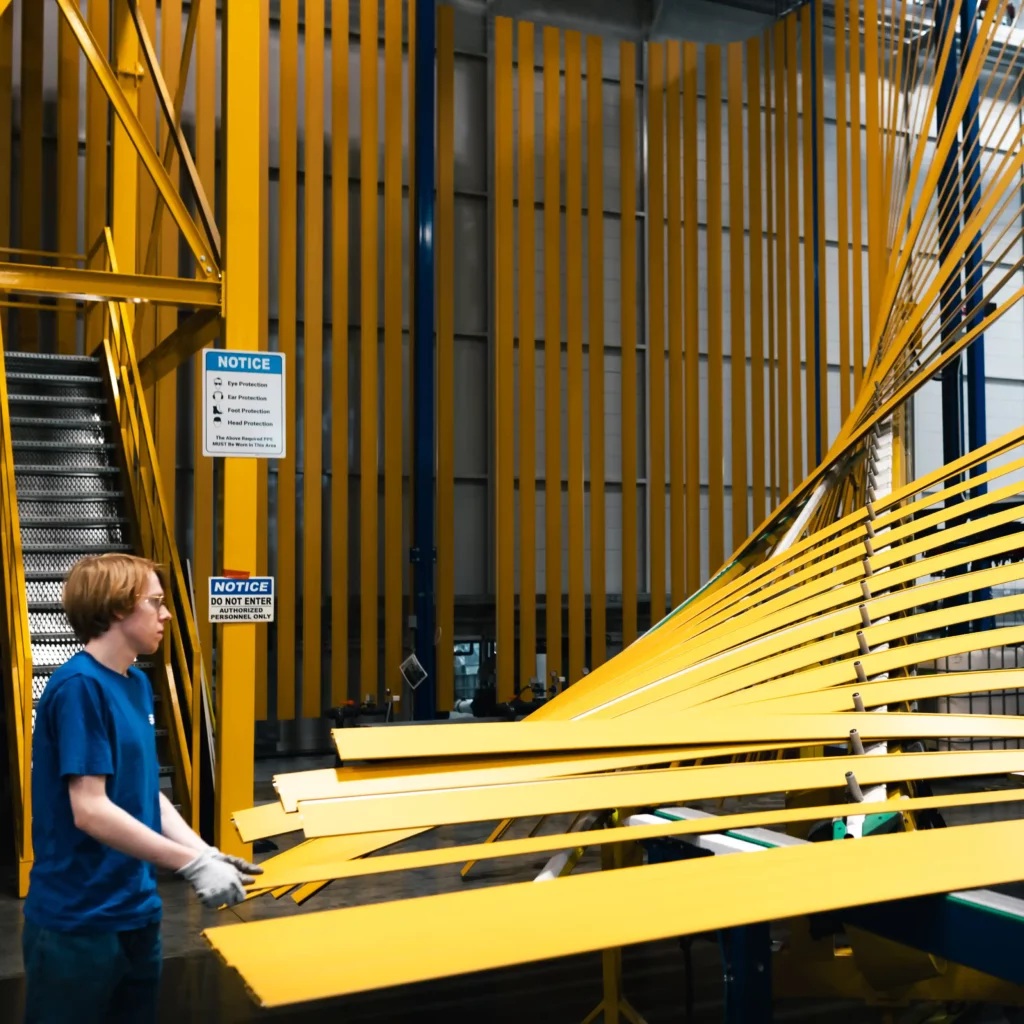
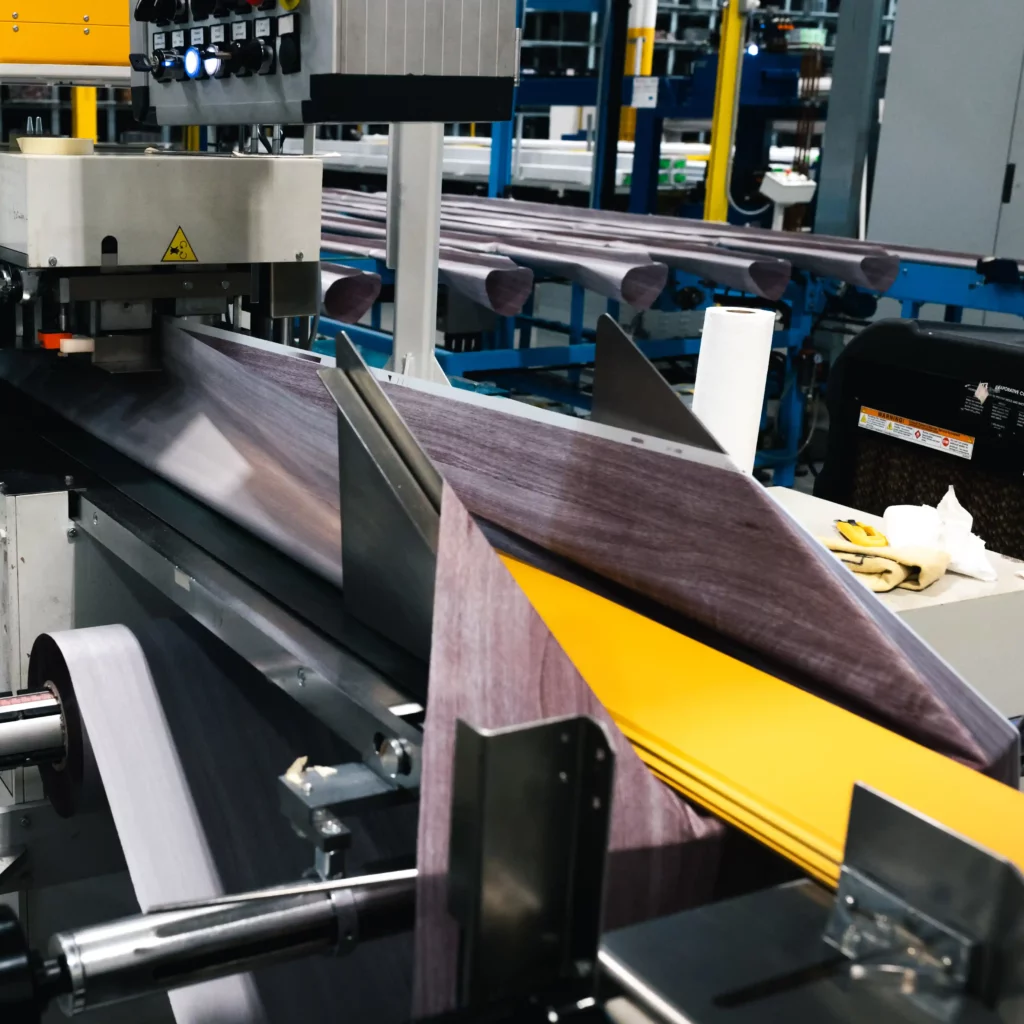
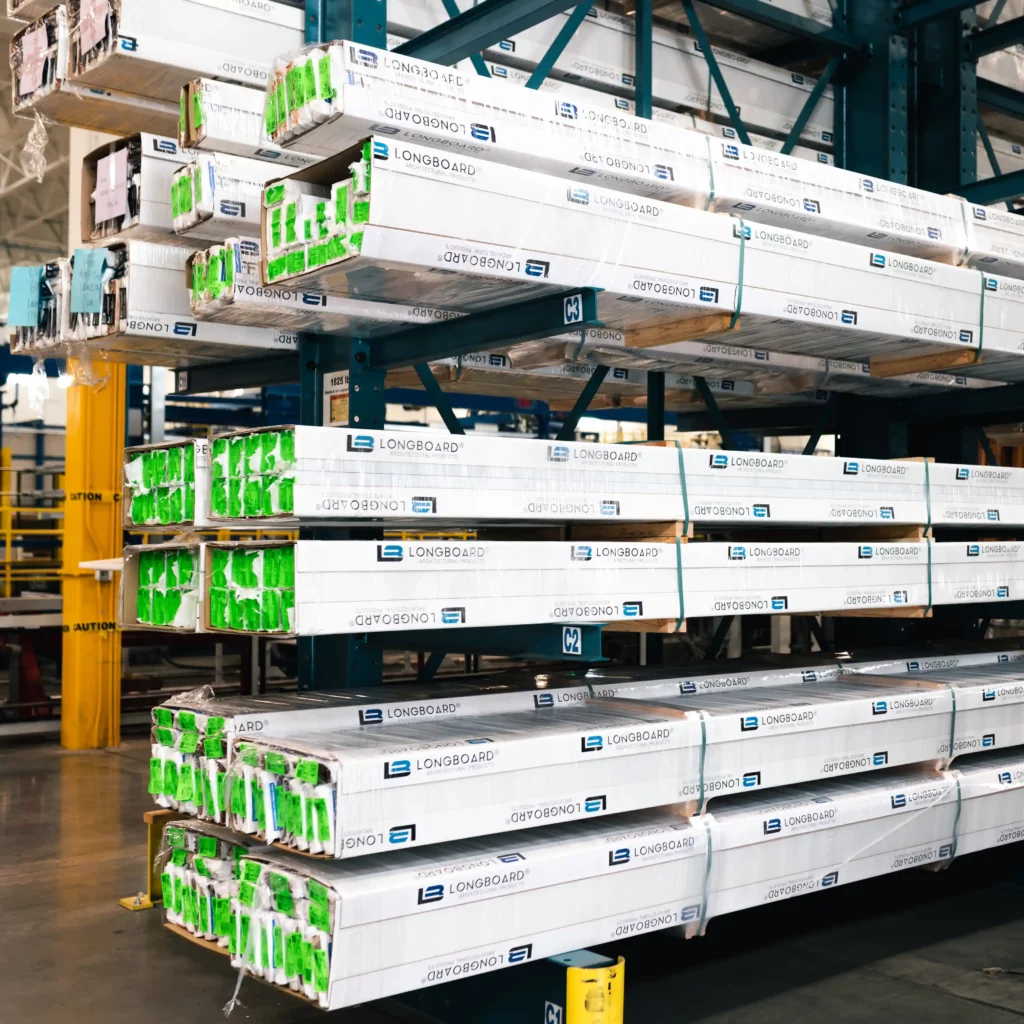
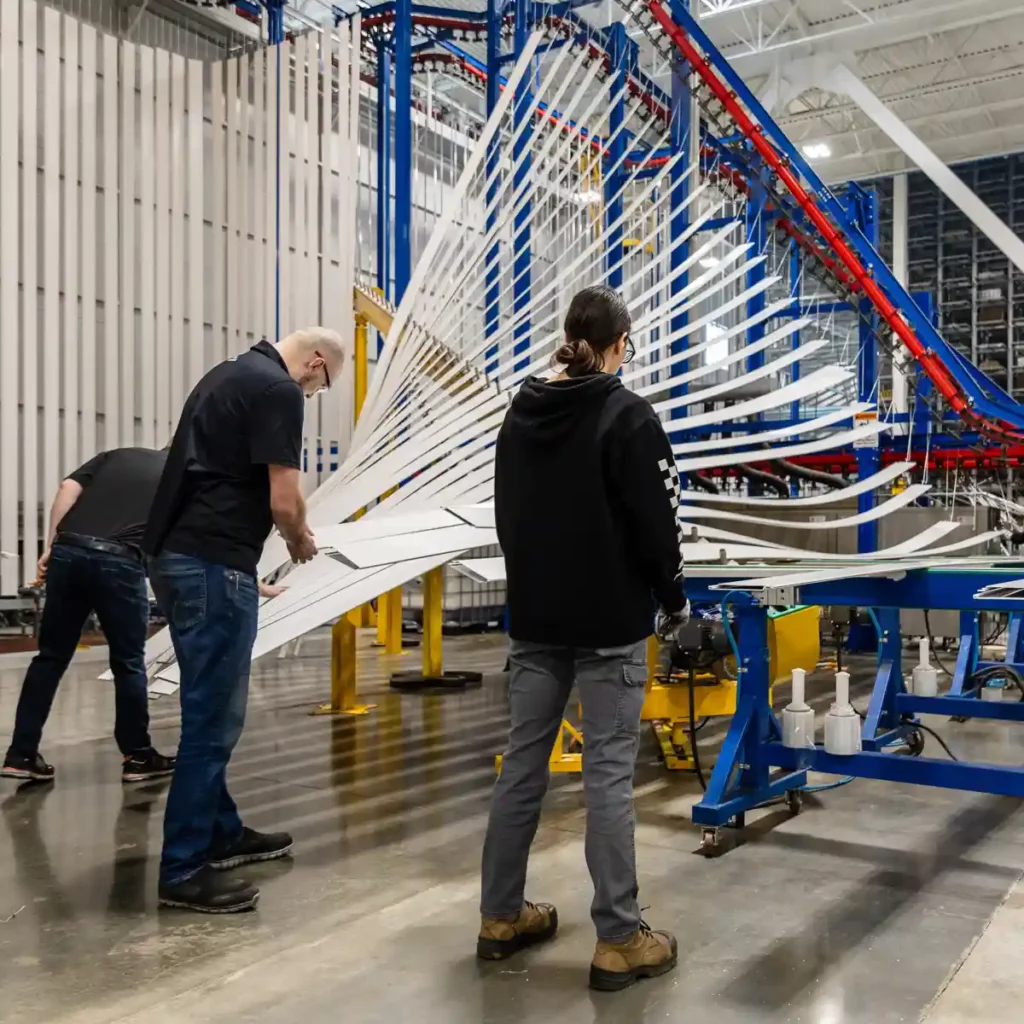
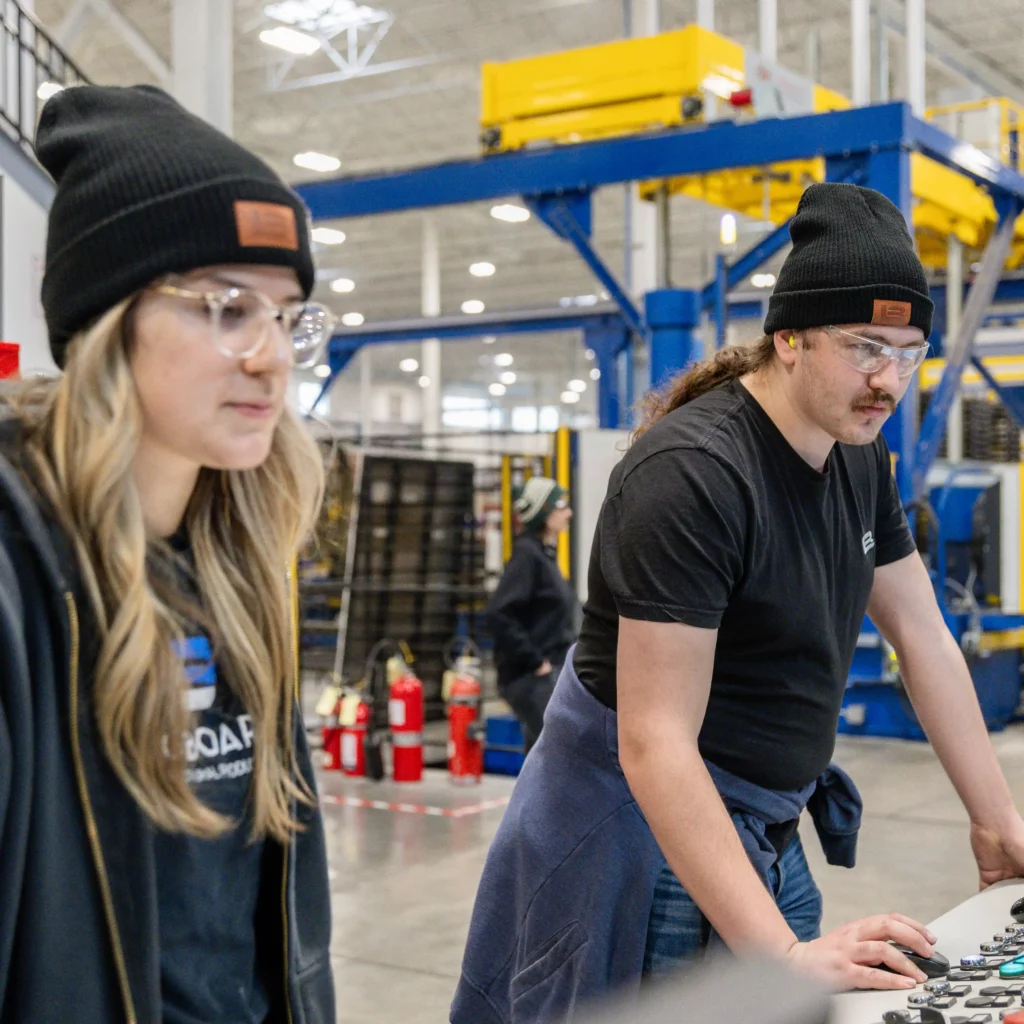
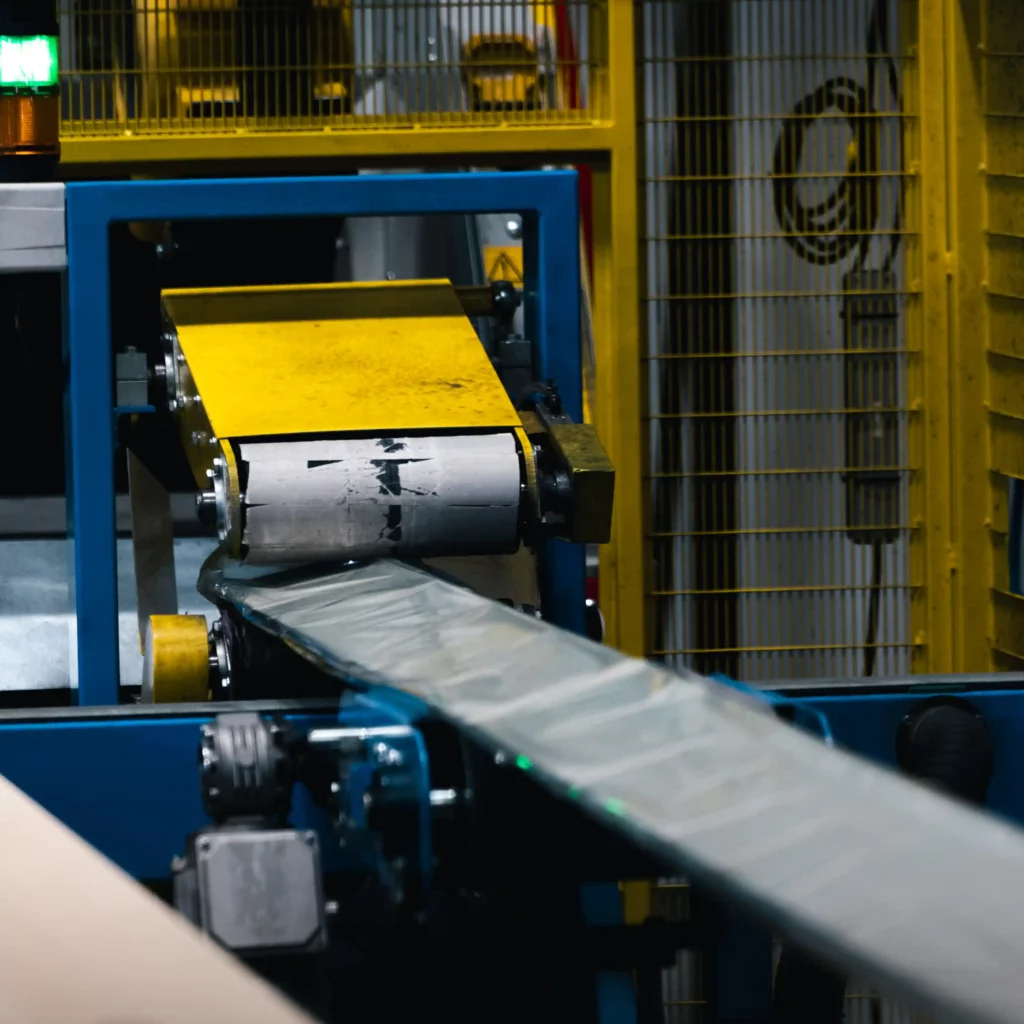
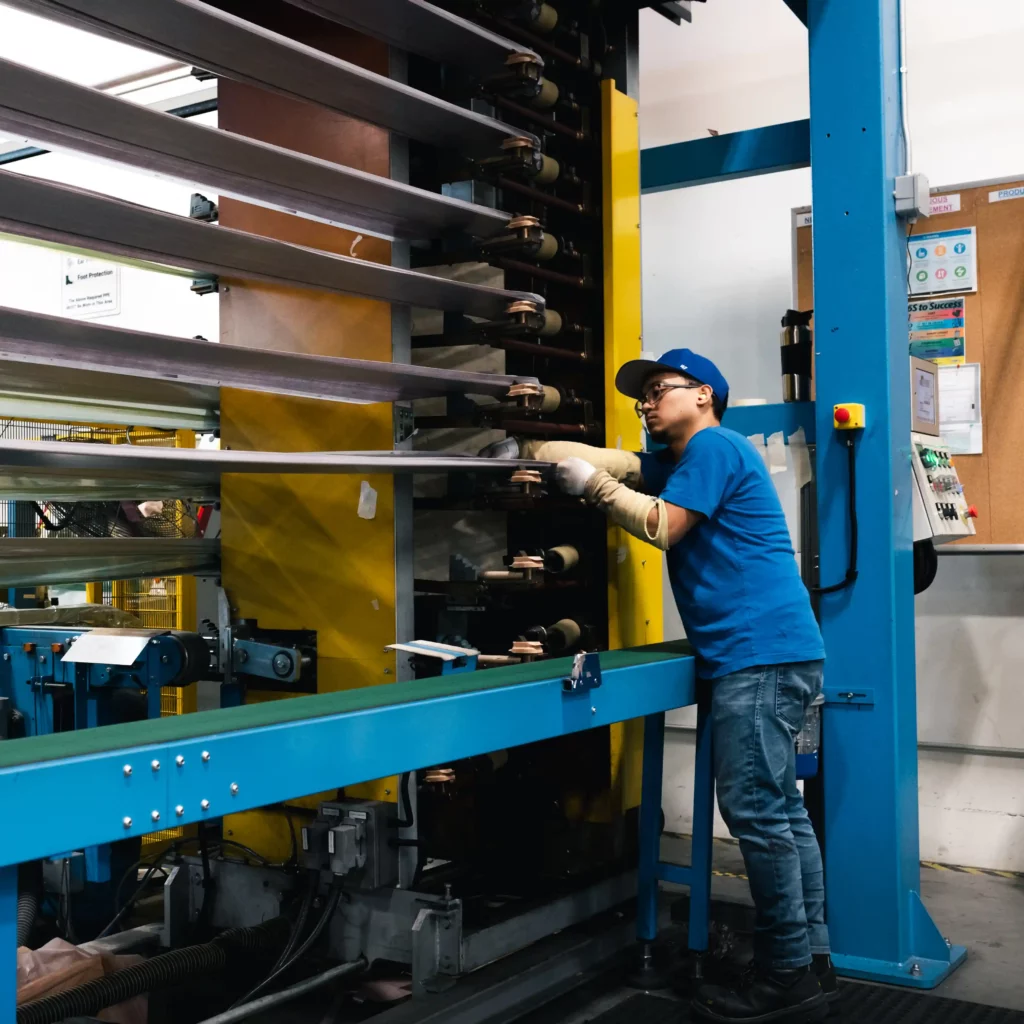
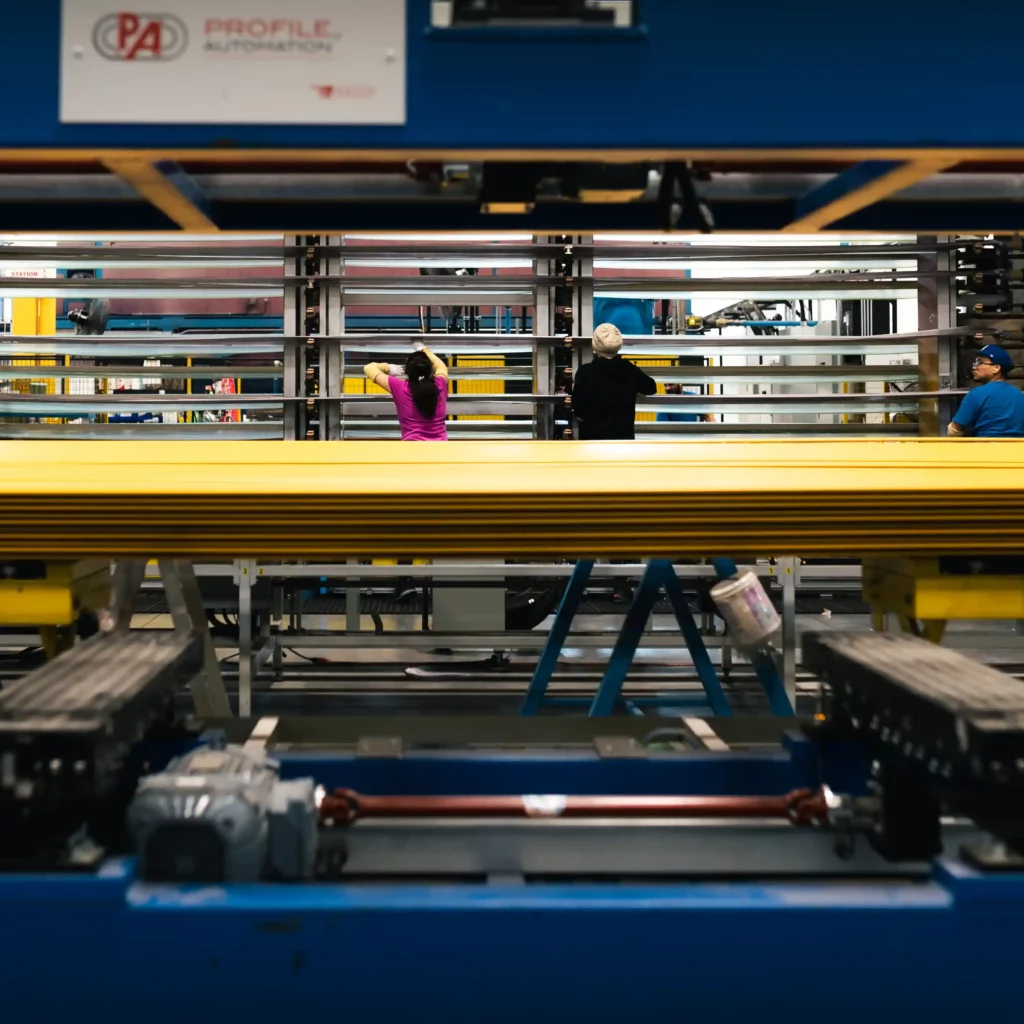
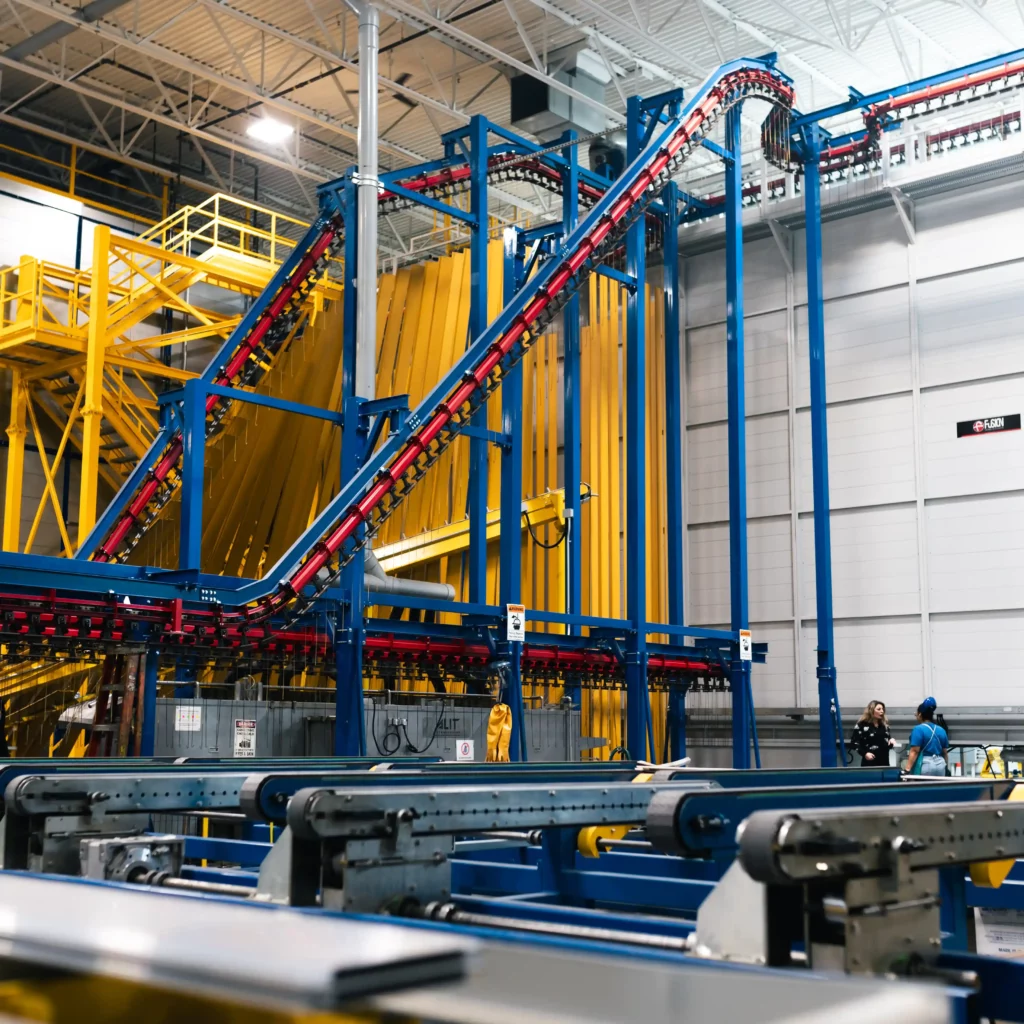
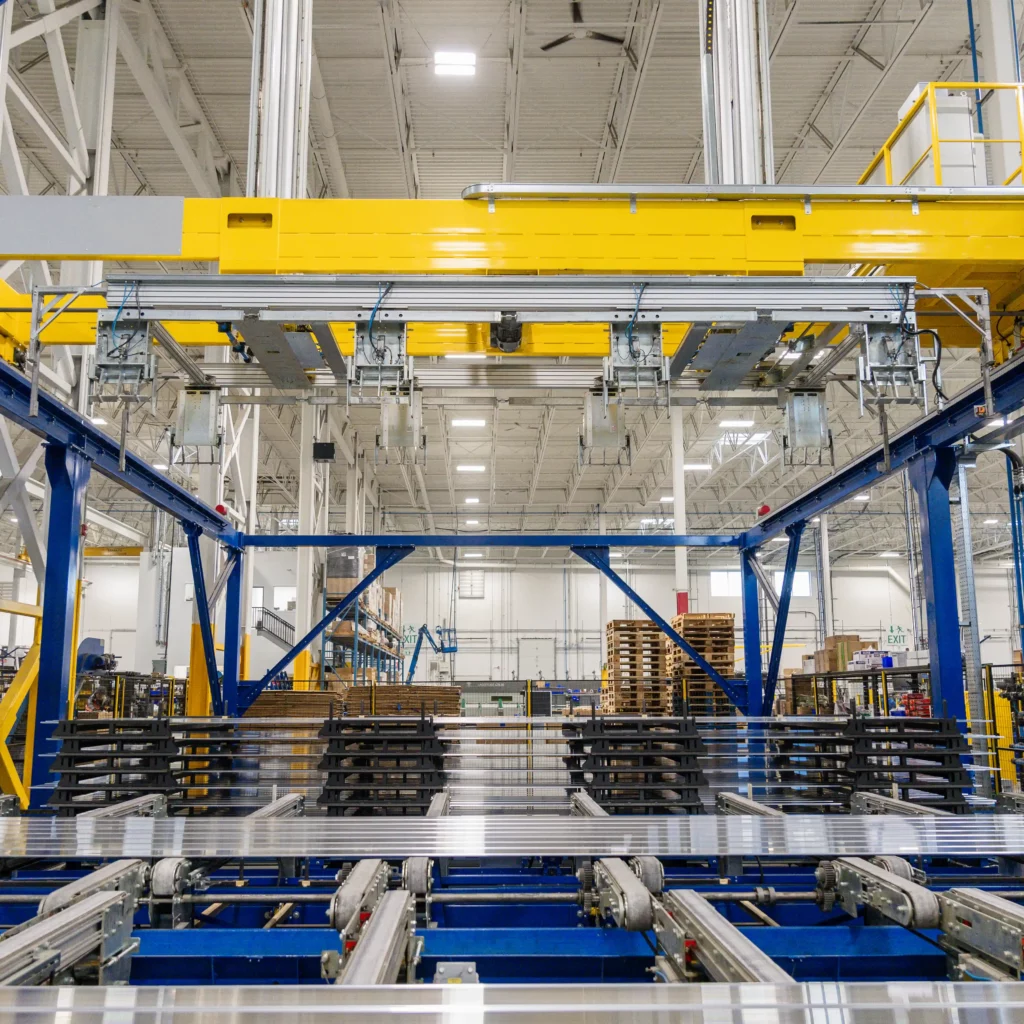
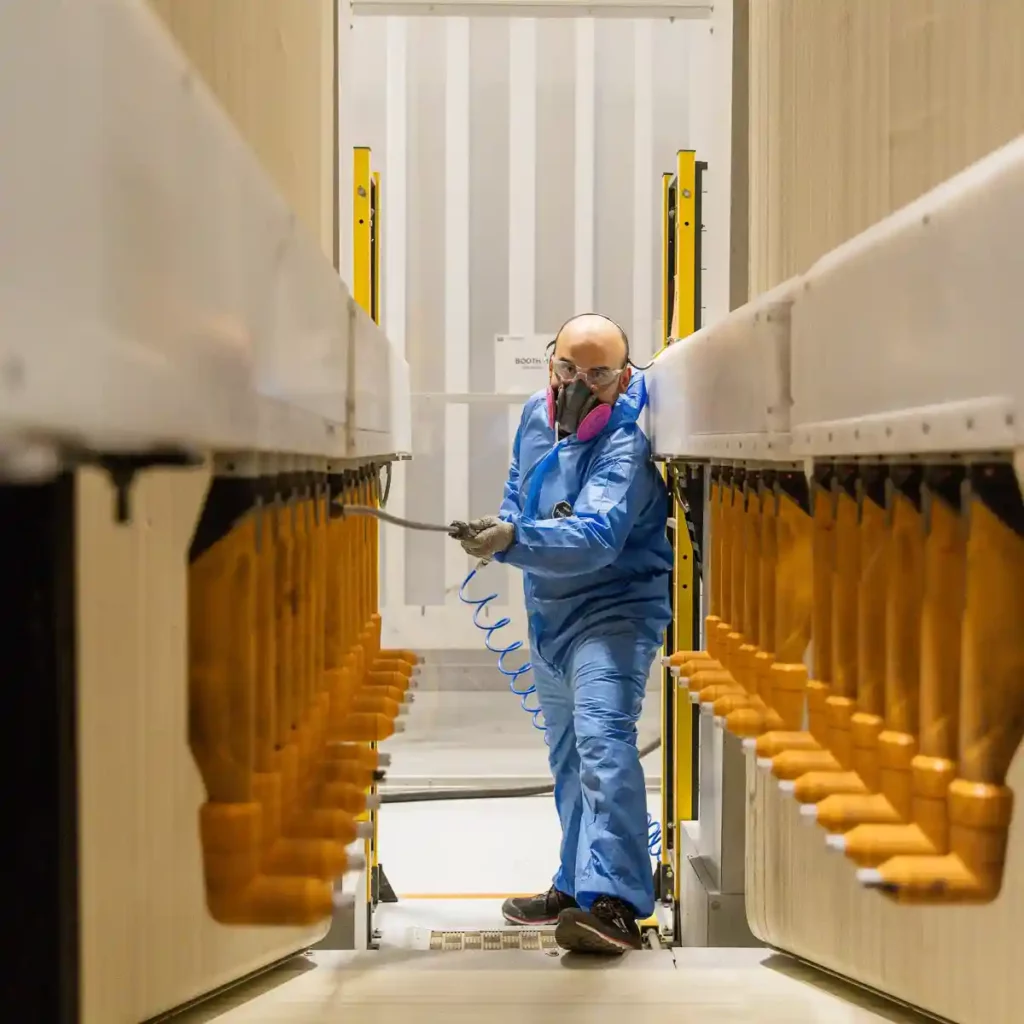
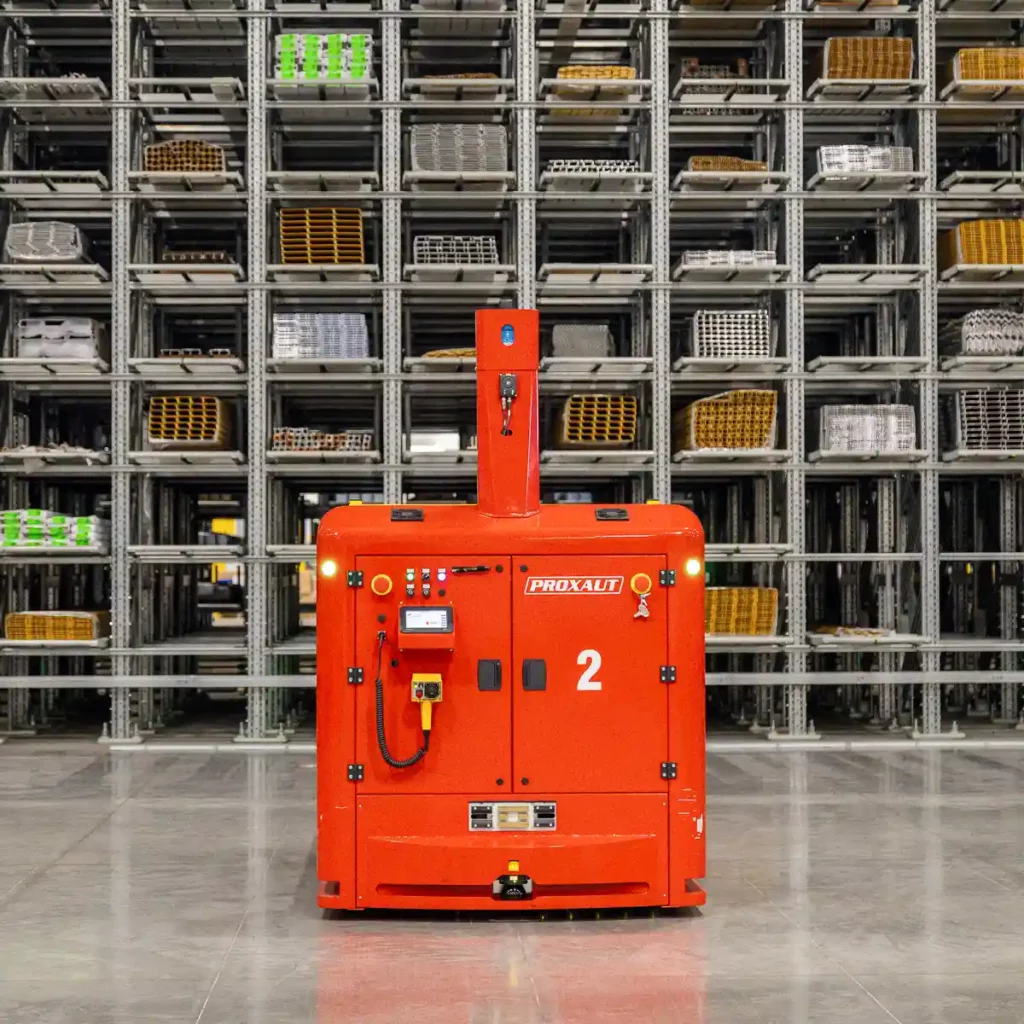