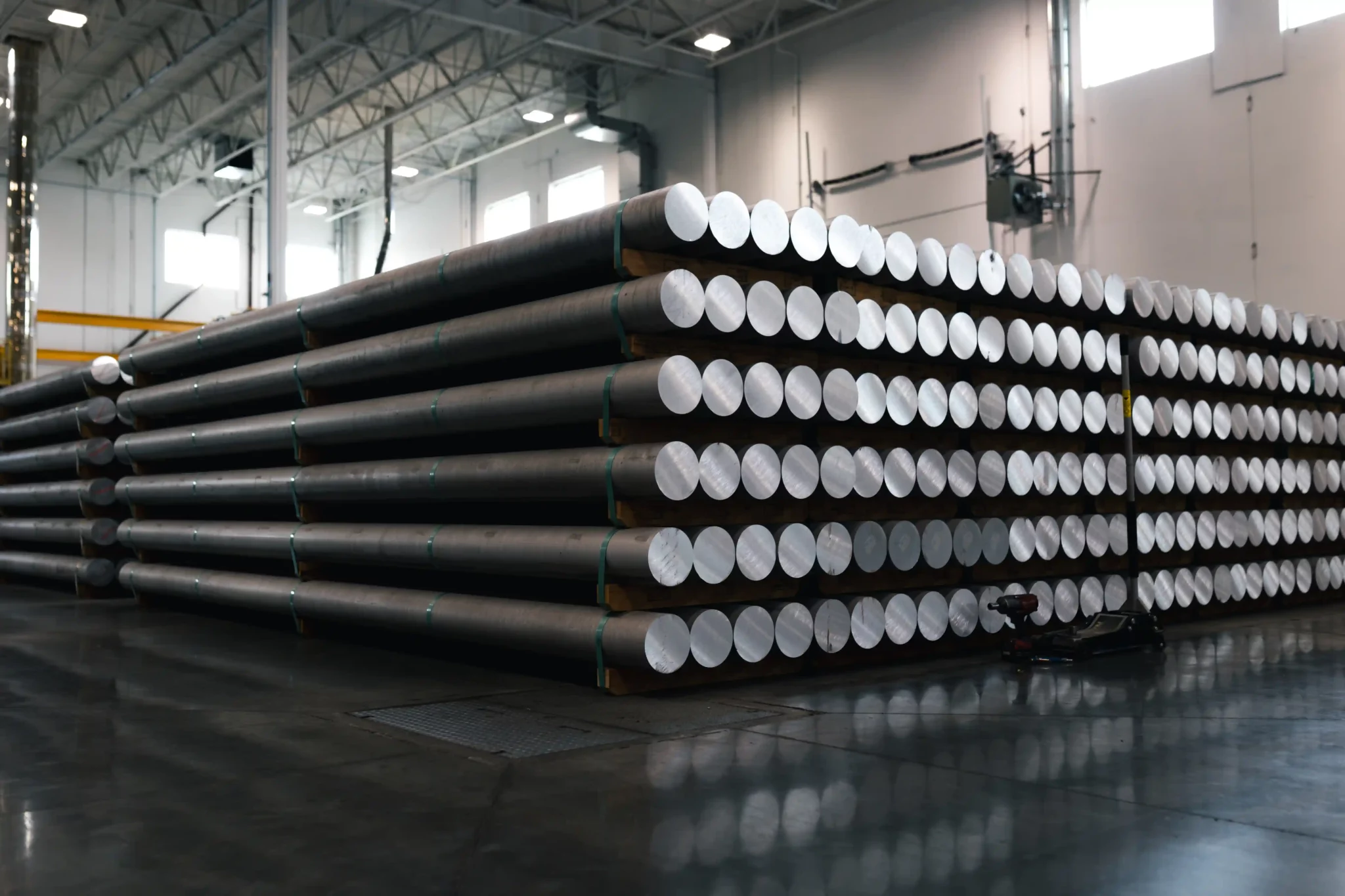
Table of Contents▶
Aluminum is often called the “green metal” of the 21st century – not because it’s inherently low-carbon to produce, but because of its critical role in enabling a more sustainable future. From lightweight components in electric vehicles and energy-efficient buildings to its infinite recyclability, aluminum is a cornerstone material for reducing emissions in other sectors. However, realizing aluminum’s full environmental benefit requires careful attention to how it’s made. This article provides an up-to-date look at the aluminum production process and the industry’s latest sustainability efforts – from mining and smelting practices in Australia and Canada to cutting-edge low-carbon technologies and high-recycled-content products like Longboard ECO™.
From Bauxite to Aluminum
Aluminum doesn’t occur in pure form in nature; instead, it’s extracted from bauxite ore. The journey from bauxite to finished aluminum involves several energy-intensive steps. Below is a brief overview of said steps. For a full in-depth process, the Australian Aluminum Council has a great interactive infographic and details of each step.
- Mining – Bauxite is strip-mined from shallow, near-surface deposits in tropical and subtropical regions. Major bauxite producers include Australia (the world’s largest, about 30% of global output) and countries in West Africa, Southeast Asia, and South America. Mining can disturb large land areas – historically involving clearing of forests and topsoil which must be carefully managed during rehabilitation.
- Refining – Mined bauxite is refined into alumina (aluminum oxide) via the Bayer process. Bauxite is dissolved at high temperature, leaving behind residues like “red mud,” a caustic waste containing impurities (e.g. arsenic, lead, and even trace radioelements)grist.org. Modern refineries treat and contain red mud securely, but it remains an environmental challenge.
- Smelting – Alumina is converted to pure aluminum metal in smelters using the Hall–Héroult process. In large electrolytic cells, alumina is dissolved in molten cryolite and electrically reduced to aluminum. This step is extremely energy-intensive, requiring ~13–15 MWh of electricity per tonne of aluminum, and it consumes carbon anodes which emit CO₂. Traditional smelting produces not only CO₂ but also perfluorocarbons (PFCs) – greenhouse gases thousands of times more potent than CO₂ – when disruptions (anode effects) occurgrist.orggrist.org. Smelting is where most of aluminum’s climate impact originates, so the carbon footprint of a smelter hinges on its power source.
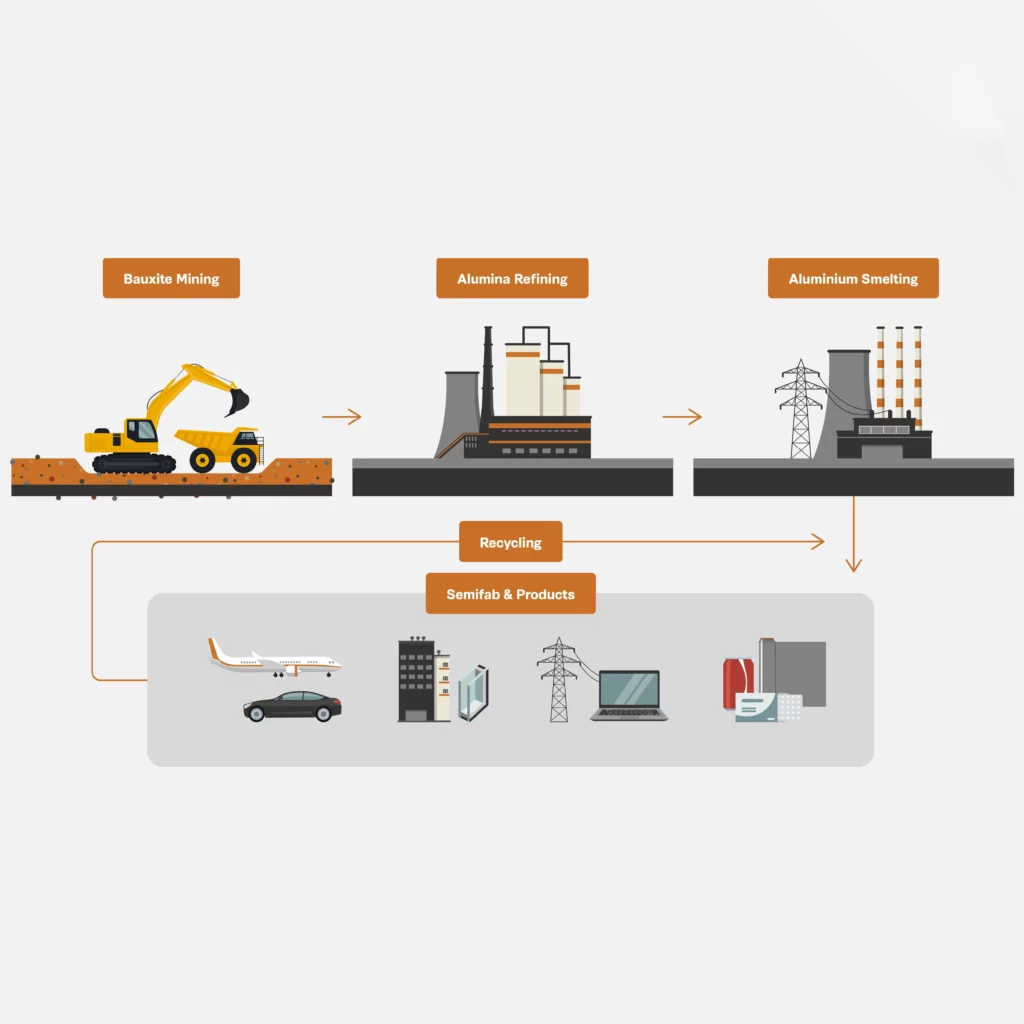
- Fabrication & Use – Raw aluminum ingots are cast and fabricated into products (sheets, extrusions, etc.) for use in construction, transportation, packaging, and technology. Aluminum’s benefits shine here: it is light, durable, corrosion-resistant, and highly recyclable, which means products can be remelted at end-of-life to avoid new primary production.
- Recycling – Aluminum can be recycled indefinitely without loss of quality. Scrap (from manufacturing off-cuts or post-consumer items) is remelted to produce new aluminum with only a fraction of the energy and emissions of primary production. We’ll explore recycling’s advantages in detail later, but it’s worth noting here: producing 1 tonne of aluminum from recycled scrap uses as little as 5% of the energy needed for primary aluminum, dramatically cutting associated carbon emissions.
Aluminum’s Carbon Footprint: A Global Comparison
While aluminum’s properties make it integral to a low-carbon economy, producing primary aluminum is still carbon-intensive. Globally, the aluminum sector emits roughly 1.1 billion tonnes of CO₂ annually (about 2% of all greenhouse gases). The majority of these emissions come from the electricity used in smelters – especially those powered by coal. According to one analysis, in 2019 about 72% of GHG emissions from primary aluminum were due to power generation. This means that where and how aluminum is made has a profound impact on its carbon footprint. Updated data as of 2024 shows a wide disparity in emission intensity (tons CO₂ per ton aluminum) among countries:
- China – By far the largest producer (~41–43 million MT in 2023), China’s aluminum industry predominantly uses coal-fired electricity. In fact, it was reported that in 2019, coal power for Chinese aluminum produced 636 million tons of CO₂, ~58% of the sector’s emissions that year. On a per-ton basis, Chinese primary aluminum can carry a carbon footprint in the range of 15+ tons CO₂ per ton (several times higher than aluminum made with hydro power). China is adding some hydro-powered smelters in provinces like Yunnan to cut this footprint, but coal remains the backbone for now. This stark contrast is why Chinese aluminum would likely face heavy tariffs under carbon border adjustment mechanisms, whereas metal from cleaner regions would not.
- India – India has risen to become the 2nd largest aluminum producer (3.97 million MT in 2023, overtaking Russia). Like China, India relies on coal power for its smelters, leading to similarly high CO₂ per ton. Indian producers such as Hindalco and Vedanta have modernized operations and improved energy efficiency, but decarbonizing will require a shift to renewables. India’s growing output – and its parallel growth in emissions – underscores the need for global best practices to spread to all major producers.
- Russia – Historically #2 in output, Russia produced about 3.7 million MT in 2023. Russian aluminum (mostly from Rusal’s smelters in Siberia) has a moderate carbon profile on average. Many Siberian smelters use hydroelectric power (e.g. Bratsk, Krasnoyarsk smelters are powered by large dams), which keeps their CO₂ per ton low – comparable to Canadian levels in some cases. However, a portion of Russian production still uses fossil-fired power or older technology. Geopolitical factors (sanctions, etc.) have also impacted the industry’s exports and modernization efforts.
- Middle East (Gulf States) – Regions like the UAE and Bahrain have become top aluminum producers by using captive natural gas power for smelters. The UAE output was ~2.66 million MT in 2023, making it #5 globally. Its primary producer (EGA) operates on natural gas, giving a carbon intensity lower than coal-based smelters but higher than hydro-based ones. Notably, in 2021 the UAE launched the world’s first commercial batch of aluminum made with solar power at EGA’s Dubai smelter. This solar aluminum (branded CelestiAL) is a small share of output so far, but it signals a shift to renewables even in oil-and-gas-rich Gulf countries. Likewise, Bahrain’s ALBA smelter, one of the world’s largest, runs on gas and is exploring solar. Middle East producers also benefit from newer, energy-efficient smelting technologies to reduce overall energy per ton.
In summary, North America, Australia, and Europe’s aluminum tends to be far cleaner than Asia’s on a per-ton basis. This has implications for manufacturers and architects seeking low-carbon materials – sourcing aluminum from places like Canada, Norway, or using recycled content can drastically cut the embodied carbon of a product. It also underpins why partnerships are forming (e.g., the U.S.-Canada initiative to share clean hydro power) to ensure metal imports meet greener standards.
Sustainable Practices in Australia and Canada
Australia is not only the top bauxite producer but also a significant aluminum producer, and it has made sustainability a priority at both ends of the process. Australian bauxite mines (in tropical Queensland, Arnhem Land, and the dry Outback of Western Australia) operate under regulations that require land rehabilitation. Mining companies like Alcoa and Rio Tinto now routinely restore mined land to natural ecosystems or other productive uses. This includes replacing topsoil, replanting native species, and even innovative measures like mulching cleared vegetation to improve soil health during rehabilitation. Thanks to these efforts, Australia’s bauxite industry aims to leave behind minimal long-term impact – a far cry from the strip-mining of decades past. On the production side, however, Australia’s aluminum smelters have historically relied on fossil-fuel power. Many Australian smelters are located near coal-fired plants (for example, in Victoria and New South Wales), which leads to a high carbon footprint for each ton of aluminum. This is driving change: there’s growing pressure to transition smelters to renewable energy or implement carbon capture. In fact, one Australian smelter (Tomago in NSW) has announced plans to gradually shift to renewable power contracts by 2029, reflecting a broader trend to decarbonize aluminum production.
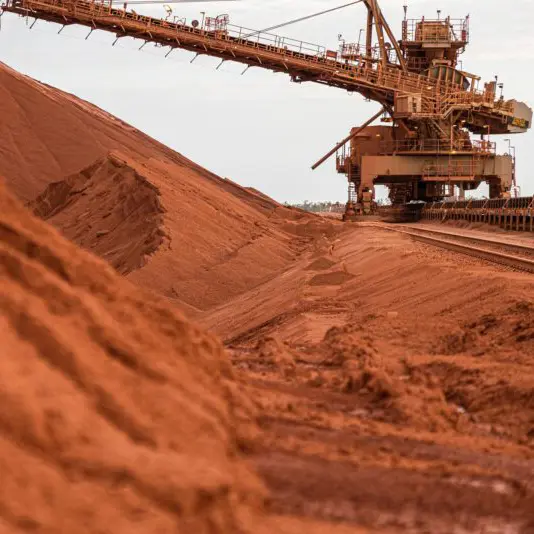
Canada, by contrast, has become a world leader in low-carbon aluminum production by leveraging abundant hydroelectric power. Around 90% of Canadian primary aluminum is produced in Quebec, where giant hydropower dams generate cheap, emissions-free electricity. As a result, Quebec’s aluminum is often called “the greenest aluminum in the world.” Nearly all smelters in Quebec (run by companies like Rio Tinto Alcan and Alcoa) operate on renewable electricity, so they emit a small fraction of the CO₂ per ton that a coal-powered smelter in Asia would. Canada produces roughly 3.1 million metric tons of primary aluminum annually (4th globally as of 2023), and it serves as the largest supplier of aluminum to the U.S.. Thanks to its low-carbon profile, Canadian aluminum is exempt from emerging carbon tariffs – for example, a future carbon border adjustment (tax on imported CO₂) would likely not penalize Canadian metal, whereas higher-carbon aluminum from elsewhere would face fees. Beyond clean energy, Canada is also pioneering smelting technology innovations (discussed later) that could eliminate the remaining direct emissions. These efforts underscore how Canada’s industry is aligning with North America’s climate goals.
It’s important to note that environmental stewardship in aluminum production extends beyond greenhouse gases. Both Australian and Canadian operations focus on reducing local pollution and ecological impacts. For instance, alumina refineries in Gladstone (Australia) and the alumina plant in Jonquière, Quebec, have improved waste management of red mud and reduced airborne pollutants like sulfur dioxide. Smelters are installing scrubbers and filters to capture fluoride and SO₂ emissions that can affect local air and water quality. These measures ensure that aluminum facilities meet strict air and water standards (in the U.S. and Canada under laws like the Clean Air Act, which, while somewhat outdated for this sector, still impose limits). In sum, countries like Australia and Canada are demonstrating that it’s possible to produce aluminum responsibly – by rehabilitating mined lands, using cleaner energy, and controlling industrial emissions.
Quebec’s Low-Carbon Aluminum & Emerging Technologies
Quebec is a bright spot on the map of sustainable aluminum – not only for its hydro powered smelters, but also for pioneering technologies that could redefine aluminum production. As noted, Quebec’s smelters already operate with an emissions profile that is a small fraction of the global average. (For perspective, producing 1 ton of aluminum in Quebec might emit around 2–3 tons CO₂, mostly from the carbon anodes, versus easily 15+ tons CO₂ in China.) But Quebec’s industry, which produces ~90% of Canada’s aluminum, isn’t resting on that advantage. Through partnerships between industry and government, it’s leading R&D that aims to eliminate carbon emissions from smelting altogether.
The flagship initiative is the ELYSIS project – a joint venture by Alcoa and Rio Tinto, with support from the governments of Canada and Quebec and companies like Apple. ELYSIS is developing inert anode technology that replaces the carbon anodes in Hall–Héroult cells with a special inert material. Instead of carbon dioxide, the cells would emit pure oxygen. In 2019, Alcoa produced the first demonstration batch of aluminum using inert anodes in Quebec (and Apple used it in some products). If successful and scaled up, inert anodes could eliminate direct CO₂ emissions from smelting – a revolutionary change for the industry. One study estimated that adopting ELYSIS technology across Quebec’s smelters could cut 6.5 million metric tons of GHG emissions per year. The potential global impact is even greater: inert anodes could eventually be adopted in smelters worldwide, especially in places with clean electricity, making truly zero-carbon aluminum possible.
Another area of innovation is carbon capture for existing smelting technology. Even as inert anodes are being piloted, some companies are looking at capturing the CO₂ from conventional smelter exhaust. Rio Tinto, for example, has researched capturing carbon from its Söderberg-cell smelters’ off-gases. While carbon capture is still in early phases for aluminum (and adds cost and energy use), it could be a retrofit solution to cut emissions at older plants if proven viable. There’s also work on alternative smelting chemistries (like the ALLUVIAL process and others) and on using biocarbon anodes instead of petroleum coke, to make the anode consumption carbon-neutral. Each of these technologies faces challenges, but they underscore a point: today’s aluminum industry is actively innovating to decarbonize further.
It’s worth mentioning that the inert anode and hydroelectric combination is essentially the holy grail for green primary aluminum. Quebec is poised to be the first jurisdiction to have it. In fact, an ELYSIS commercial cell is under construction in Saguenay, QC, and by 2024–2025 we expect the first industrial aluminum made with zero direct CO₂ emissions. This not only cements Quebec’s leadership in clean aluminum, but provides a template for other regions. If Iceland, Canada, Norway – and even parts of China – adopt similar technology where renewable power is available, aluminum’s global carbon footprint could decline dramatically in the coming decades, even as demand for the metal grows.
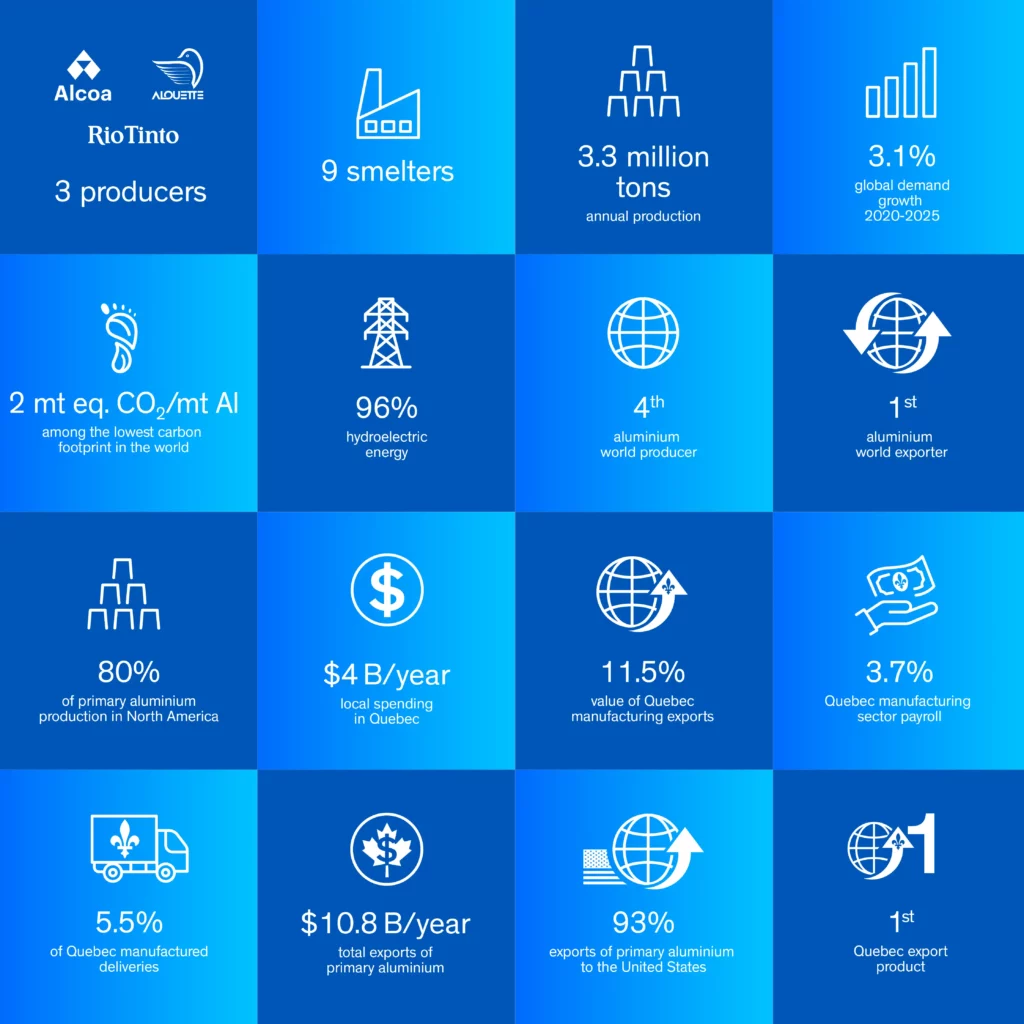
Recycling: Aluminum's Key to Sustainability
One of aluminum’s greatest contributions to a cleaner world is its recyclability. Unlike many materials, aluminum can be recycled repeatedly without degrading in quality, forming a true closed-loop cycle. This is crucial because producing secondary aluminum (from scrap) uses only a fraction of the energy required for primary production. In fact, recycling aluminum saves about 95% of the energy and emissions compared to making new aluminum from bauxite. This huge energy savings translates directly into climate benefits: remelting scrap avoids mining and refining, and it largely eliminates the CO₂ from electrolysis (since you’re not reducing oxide with carbon anodes in the same way). Some updated figures underscore the environmental impact of recycling:
- Energy and Emissions Savings: Manufacturing 1 tonne of aluminum from recycled scrap (also called secondary aluminum) can avoid around 11–13 tonnes of CO₂ emissions that would have been generated producing that tonne from ore, according to industry analyses. The World Economic Forum notes that currently about 73% of used aluminum is recycled globally, and raising that rate to 95% would reduce the need for primary aluminum by 15% – preventing an estimated 250 million metric tons of CO₂ per year. That annual CO₂ saving is roughly equivalent to the entire emissions of a country like Spain. In short, every can or window frame that gets recycled instead of landfilled makes a real difference.
- Resource Conservation: Recycling one tonne of aluminum saves about 4 tonnes of bauxite ore and over 1 tonne of alumina (since those inputs are no longer needed). It also means avoiding the caustic red mud waste and other pollutants from those stages. By keeping aluminum in circulation, we reduce the pressure to expand mining into new areas. (Notably, the aluminum industry is working on recycling more than just manufacturing scrap; a priority is boosting end-of-life recycling from products like old cars, buildings, and appliances. In the U.S., less than half of recycled aluminum currently comes from old used products – there’s plenty of room to improve by capturing more aluminum from vehicles, for example.)
- Economic Benefits: Recycling aluminum is not only green but cost-effective. The energy saved translates to lower production costs, which is why recycling has long been integral to the aluminum industry. North America’s secondary aluminum sector is robust – many facilities remelt scrap (cans, extrusion off-cuts, etc.) to make new ingots or billet. This supports jobs in recycling and reduces the need for imported metal. According to the Aluminum Association, the U.S. aluminum recycling industry employs tens of thousands of workers and significantly cuts domestic energy use.
For architects, builders, and product manufacturers, using high-recycled-content aluminum is a smart way to reduce embodied carbon. Common aluminum building products (like cladding, panels, window frames) often contain a large recycled fraction already (sometimes 50% or more is recycled content). Each percentage point increase in recycled content directly lowers the CO₂ footprint of the material.
Specifying products made from recycled or “low-carbon” aluminum can contribute to green building certification credits (under LEED v4, for instance, recycled content contributes to Material & Resources credits). As the Environmental Integrity Project recently emphasized, expanding aluminum recycling and using that scrap in new projects is one of the most immediate steps to mitigate climate impacts of the aluminum supply chain.
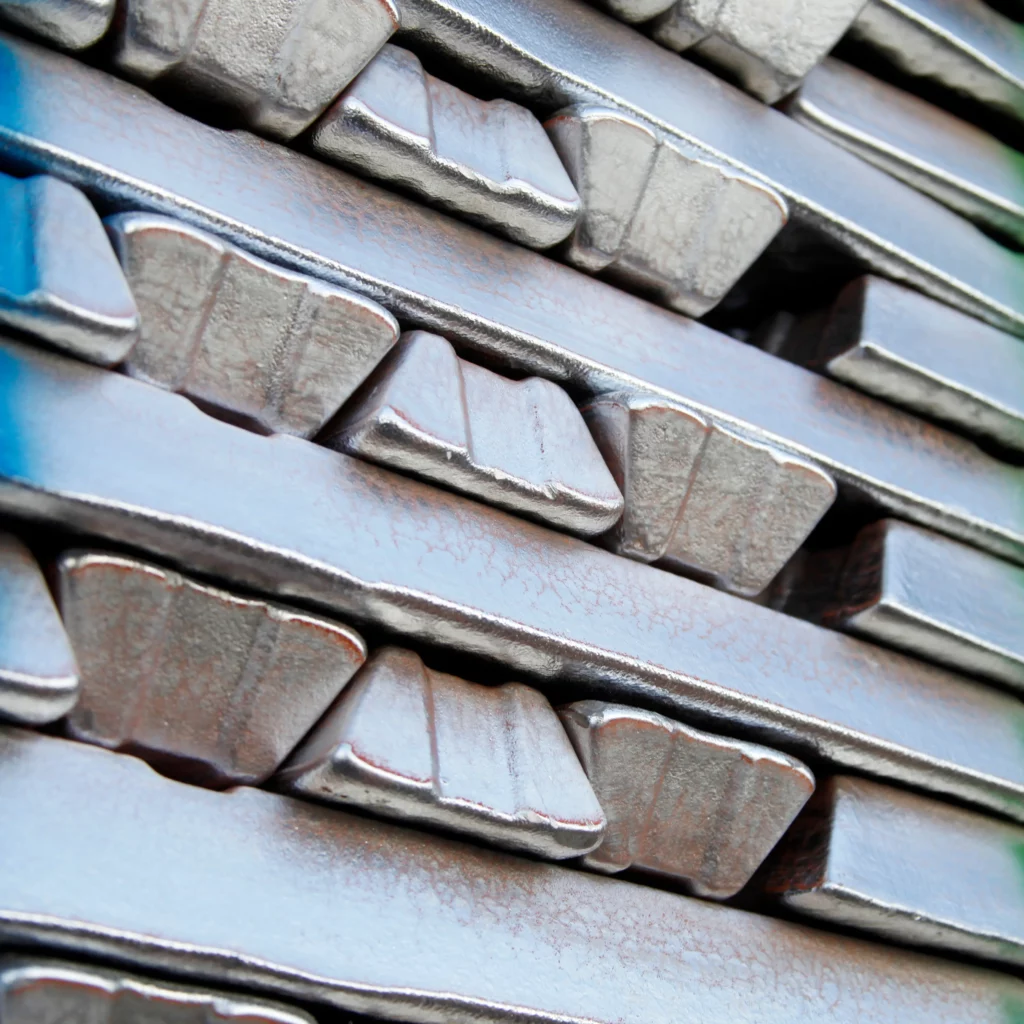
Longboard ECO™: High-Recycled, Low-Carbon Aluminum for Buildings
With the above context, it’s clear that using low-carbon and recycled aluminum is a key strategy in sustainable construction. This is precisely the idea behind Longboard ECO™, a product line by Longboard® Architectural Products that exemplifies aluminum’s contribution to greener building in North America. Longboard ECO™ is a suite of aluminum cladding and siding products made with a high recycled content, resulting in an embodied carbon footprint less than 50% of the industry average. In February 2022, Longboard announced the ECO line as part of its commitment to sustainable innovation, ensuring the ECO products meet the same performance and quality standards as its regular offerings. Each Longboard ECO™ product comes with verified life-cycle assessments and Environmental Product Declarations (EPDs) to transparently show its impacts.
For architects and developers, specifying Longboard ECO™ can directly help in achieving green building certifications:
- LEED® v4/v4.1 Credits: Longboard ECO’s recycled content and low embodied carbon can contribute to LEED materials credits. Mike Heppell, Longboard’s President, noted that these products “provide architects…a sustainable option in reducing embodied carbon, obtaining LEED certification, and make achieving net-zero emissions attainable.” The company has documented which LEED credits apply to its systems (e.g. Building Life-Cycle Impact Reduction, Recycled Content, and Optimization of Environmental Product Declarations), making it easier for project teams to use Longboard in green designs.
- WELL Building Standard: Aluminum is an inert, non-off-gassing material. Longboard products are finished with powder coat that is VOC-free and Red List-free (no harmful chemicals), which supports healthy indoor environments. While WELL certification focuses on occupant health, using materials that emit zero VOCs and contain no toxic ingredients (like Longboard’s finishes) aligns with WELL requirements for healthy material selection. Additionally, Longboard’s aluminum is non-combustible and doesn’t support mold growth, contributing to indoor air quality – another WELL concern.
- Environmental Management Certifications: Longboard has demonstrated its commitment to environmental responsibility in manufacturing. The company’s facility is ISO 14001 certified for environmental management (alongside ISO 9001 for quality), meaning it adheres to strict standards to minimize waste, pollution, and resource use. In practice, Longboard’s factory in Abbotsford, BC uses over 90% hydroelectric power to run its operations, cutting down on fossil energy. All aluminum scrap and off-cuts from production are melted down and reused on-site, creating a closed-loop system with essentially zero aluminum waste. Water used in extrusion and coating processes is treated and recycled, and even rainwater is captured for use in pretreatment. These actions not only earn certifications, but tangibly reduce the environmental footprint of each Longboard product.
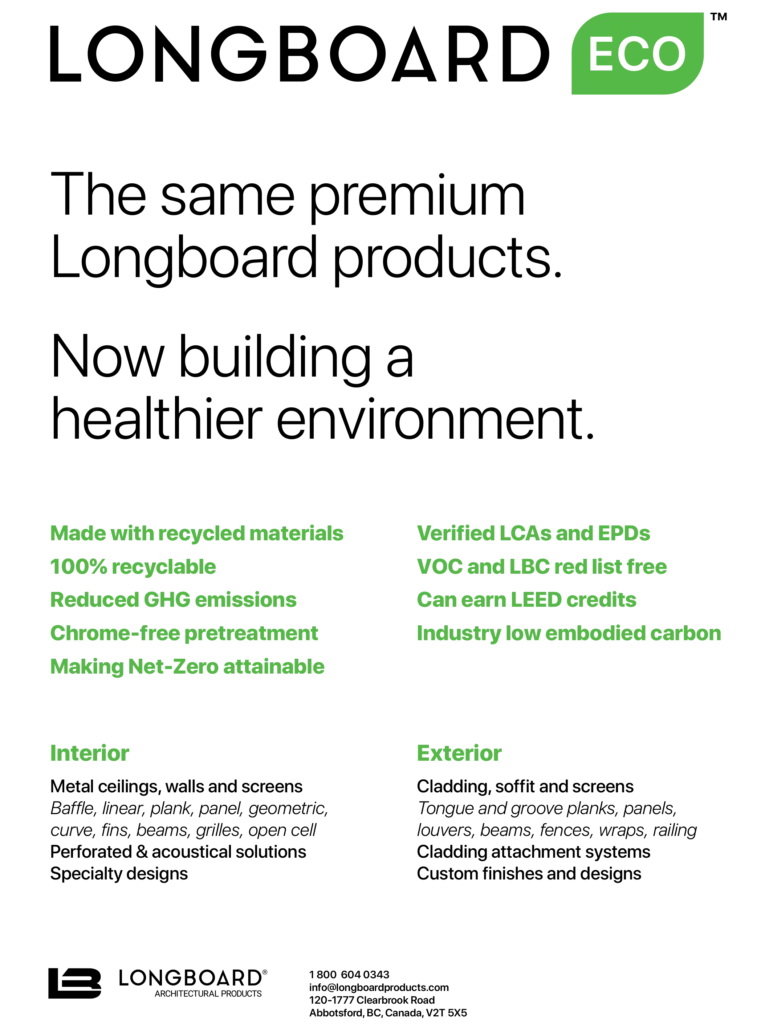
Longboard ECO™ products integrate seamlessly with sustainable design goals. They offer the same sleek aesthetics, durability, and low maintenance of standard Longboard aluminum cladding – but with a significantly reduced carbon footprint. For example, if a typical aluminum façade panel has an embodied carbon X (due to some mix of primary metal in it), an ECO™ panel would be less than half of X in CO₂ emissions. Using these products can help projects achieve Net-Zero Carbon targets for materials. As Heppell stated, “This is a true innovation in our industry and underscores our commitment to…building a sustainable future.” By choosing high-recycled-content aluminum, architects are effectively leveraging that 95% energy savings of recycling at a product level – the more recycled metal, the less new aluminum had to be smelted, and the fewer emissions to account for.
Finally, it’s important to highlight that aluminum itself contributes to longevity and energy efficiency in buildings, which is another aspect of “a cleaner North America.” Aluminum cladding and soffits, like Longboard’s, are highly durable (resistant to rot, rust, and fire) and virtually maintenance-free, reducing the need for painting or replacement. This long service life means less frequent material replacement over a building’s lifespan – conserving resources. Aluminum building products also often facilitate better envelope performance (for instance, façade panels can be part of rainscreen systems that improve insulation and moisture management). All these factors play into sustainability. Longboard’s Quick Screen™ attachment system, for example, simplifies installation and allows components to be reused or recycled at end of life.
In summary, Longboard ECO™ exemplifies how the aluminum industry is proactively aligning with green building trends. By drastically lowering embodied carbon and providing transparent documentation (EPDs, LCAs), it enables project teams to make informed, sustainable choices without sacrificing design or performance. The aluminum in Longboard ECO™ is not only contributing to a cleaner North America – it’s also manufactured in North America under clean, responsible practices, amplifying the local environmental benefits.
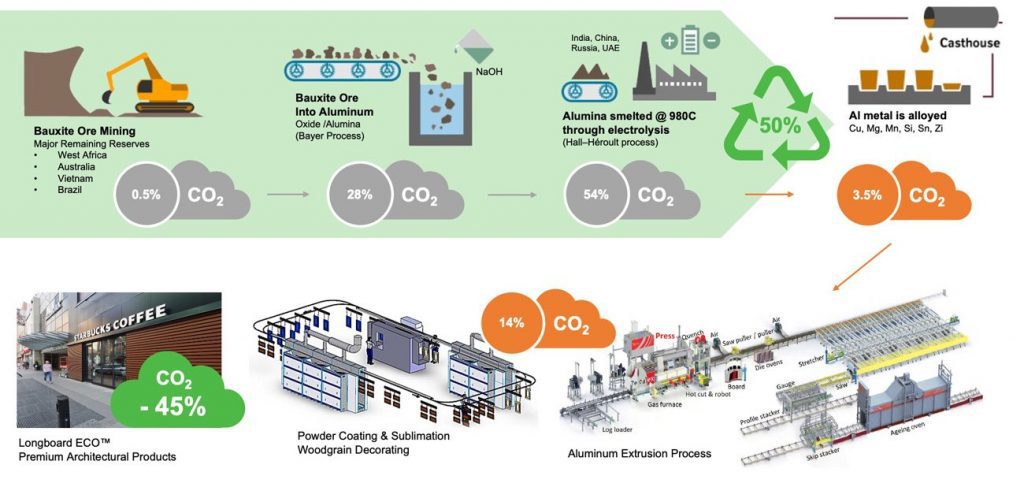
Wrapping Up
Aluminum has a unique dual role in sustainability: it is an enabler of low-carbon solutions (lightweight structures, EVs, solar panels, etc.) and it is a material whose own production must continually evolve to be cleaner. As we’ve seen, the aluminum sector in North America and beyond is meeting this challenge head-on. Modern mining rehabilitation in Australia, hydropowered low-carbon smelting in Canada, and increased recycling everywhere are reducing aluminum’s environmental footprint today. On the horizon, technological breakthroughs like inert anodes promise an even more dramatic decarbonization of aluminum production, ensuring that as demand for this versatile metal grows, emissions do not grow with it.
For architects, builders, and manufacturers in North America, these developments mean that using aluminum – especially products with recycled content or low-carbon pedigree – can significantly cut the embodied energy and emissions of projects. With products like Longboard ECO™, one can specify aluminum that is not only high-performance and beautiful, but also verified as environmentally superior. Such choices support broader certification goals (LEED, WELL, etc.) and ultimately contribute to cleaner air and lower CO₂ emissions in our communities.
In the quest for sustainable development, aluminum is part of the solution. It allows us to build lighter, last longer, and recycle endlessly. And thanks to industry efforts in making its production cleaner – from the mines of the Outback to the smelters of Quebec – aluminum is increasingly aligned with the climate-conscious future that North America is striving for. Every coil, sheet, or extrusion of aluminum that comes with a lower carbon tag is a building block of that cleaner future. In that regard, aluminum truly is contributing to a cleaner North America, and the progress continues year by year.
If you’d like to learn more, we offer a AIA accredited presentations regarding “Reducing Carbon Emission Using Aluminum” and “Using Aluminum Extrusions to Create Sustainable Façades “. Use the form at the link below to schedule a presentation with your regional representative.